Multipurpose vacuum casting device
A multi-purpose, vacuum smelting technology, applied in the field of metallurgy, can solve the problems of limited popularization and application, and the inability to realize vacuum pouring and continuous casting, and achieve the effects of reducing manufacturing costs, reducing volume, and improving mold filling capabilities
- Summary
- Abstract
- Description
- Claims
- Application Information
AI Technical Summary
Problems solved by technology
Method used
Image
Examples
Embodiment 1
[0017] Embodiment 1: Vacuum induction heating melting
[0018] First remove the plugging mechanism 6 for continuous casting, the induction coil 7 for continuous casting, the crucible 8 for continuous casting, the crystallizer 9 and the annular circulating water jacket 10 for primary cooling, and adopt the double-layer seal ring 11 to seal the furnace of the smelting furnace 4 At the bottom, then put the purity of 99.99% electrolytic nickel and 99.99% oxygen-free copper into the melting crucible 19 according to the mass percentage of Ni30% and Cu70%, with a total mass of 25kg. Start the vacuum system 12, and the vacuum degree reaches 0.1Pa; then gradually adjust the current, the alloy sample is gradually melted under the action of the induction coil 20 for melting, the temperature of the melt is observed through the thermocouple, and the melting condition of the alloy is checked through the observation port 5 of the furnace cover , after the alloy is completely melted, start th...
Embodiment 2
[0019] Embodiment 2: Vacuum pouring
[0020]First remove the plugging mechanism 6 for continuous casting, the induction coil 7 for continuous casting, the crucible 8 for continuous casting, the crystallizer 9 and the annular circulating water jacket 10 for primary cooling, and adopt the double-layer seal ring 11 to seal the furnace of the smelting furnace 4 Then adopt vacuum induction heating smelting as in Example 1, put the pure chromium that 99.95% quality is 1kg into the alloy feeding hopper 17 with the purity of 99.95%, put the oxygen-free copper that 10kg purity is 99.99% into the crucible for smelting In 19, melt at 1400°C, observe the melt temperature through a thermocouple and check the melting condition of oxygen-free copper through the observation port 5 of the furnace cover. After the oxygen-free copper is completely melted, open the alloy feeding hopper 17, and put pure chromium into the smelting In the crucible 19, then start the liftable electric stirring mechan...
Embodiment 3
[0021] Example 3: BFe10-1-1 cupronickel alloy wire with an outer diameter of 6.0 mm formed by vacuum smelting and continuous casting under argon protection
[0022] First dismantle the induction coil 20 for smelting, launder 22 and the movable liquid launder 23 with heater, and close the vacuum slide valve 24; and 99.99% oxygen-free copper are placed in the crucible 8 for continuous casting according to the mass percentage of Ni10%, Fe1.0%, Mn0.5%, and Cu balance, and then start the vacuum system 12, and the vacuum degree reaches the required value; Then start the primary cooling annular circulating water jacket 10 and the secondary cooling circulating water spray device 13, and start the power supply device 1, and use the artificial intelligence control instrument 3 to precisely control the temperature. After the raw materials are completely melted at 1250°C, start the inert protective gas source 14 , fill in argon protective gas, keep the pressure in the smelting furnace 4 i...
PUM
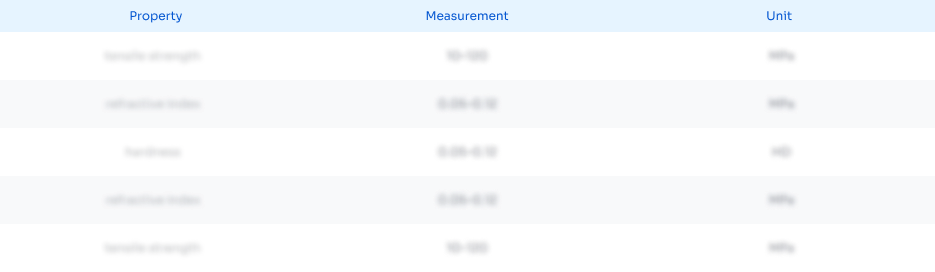
Abstract
Description
Claims
Application Information

- R&D
- Intellectual Property
- Life Sciences
- Materials
- Tech Scout
- Unparalleled Data Quality
- Higher Quality Content
- 60% Fewer Hallucinations
Browse by: Latest US Patents, China's latest patents, Technical Efficacy Thesaurus, Application Domain, Technology Topic, Popular Technical Reports.
© 2025 PatSnap. All rights reserved.Legal|Privacy policy|Modern Slavery Act Transparency Statement|Sitemap|About US| Contact US: help@patsnap.com