High-strength electro-conductive copper alloy wire and production method thereof
A conductive wire material and production method technology, applied in metal rolling, temperature control, metal rolling, etc., can solve problems such as low tensile strength and heat resistance, human body and environmental pollution, and large market demand, and achieve Effect of promoting dispersion, improving heat resistance, and good overall performance
- Summary
- Abstract
- Description
- Claims
- Application Information
AI Technical Summary
Problems solved by technology
Method used
Examples
Embodiment 1
[0024] The composition produced by the aforementioned process is an alloy of Mg: 0.41%, Ni: 0.45%, Si: 0.12%, Zr: 0.09%, and copper as the balance. After the alloy is melted, it is continuously cast at a speed of 0.17m / min at a constant temperature of 1220°C to cast a Ф16mm wire billet, after peeling, annealing, cold drawing, solution treatment (Ф1.2mm, 850°C×0.5h), cold drawing, Aging treatment (Ф0.4mm, 450℃×1h) and cold drawing, the performance is σ at the finished size of Ф0.1mm b : 770MPa, δ 10 : 6.5%, %IACS: 63, one-way twist: 36 times;
Embodiment 2
[0026] The composition produced by the aforementioned process is an alloy of Mg: 0.45%, Ni: 0.43%, Si: 0.1%, Zr: 0.12%, and copper as the balance. After the alloy is melted, it is continuously casted at a speed of 0.16m / min at a constant temperature of 1200°C, with a wire billet of Ф16mm. After peeling, annealing, cold drawing, solution treatment (Ф1.2mm, 850°C×0.5h), cold drawing, Aging treatment (Ф0.4mm, 450℃×1h) and cold drawing, the performance is σ at the finished size of Ф0.1mm b : 760MPa, δ 10 : 5%, %IACS: 65, one-way twist: 35 times;
Embodiment 3
[0028] The composition produced by the aforementioned process is an alloy of Mg: 0.2%, Ni: 0.8%, Si: 0.2%, Zr: 0.15%, and copper as the balance. After the alloy is melted, the Ф40mm billet is continuously cast at a speed of 0.1m / min at a constant temperature of 1160°C. After rolling, peeling, annealing, cold drawing, solution treatment (Ф1.2mm, 850°C×0.5h), cold Drawing, aging treatment (Ф0.4mm, 450℃×1h) and cold drawing, the performance is σ when the finished product size is Ф0.1mm b : 790MPa, δ 10 : 5%, %IACS: 61, one-way twist: 30 times;
PUM
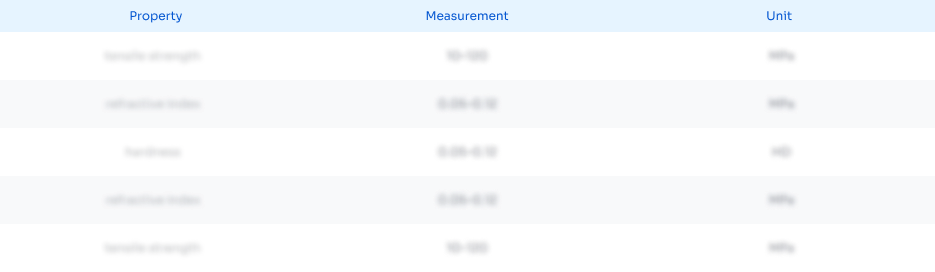
Abstract
Description
Claims
Application Information

- R&D
- Intellectual Property
- Life Sciences
- Materials
- Tech Scout
- Unparalleled Data Quality
- Higher Quality Content
- 60% Fewer Hallucinations
Browse by: Latest US Patents, China's latest patents, Technical Efficacy Thesaurus, Application Domain, Technology Topic, Popular Technical Reports.
© 2025 PatSnap. All rights reserved.Legal|Privacy policy|Modern Slavery Act Transparency Statement|Sitemap|About US| Contact US: help@patsnap.com