Method for preparing modified anode material of lithium ion battery
A technology for lithium-ion batteries and cathode materials, which is applied in the field of preparation of lithium-ion battery materials, can solve the problems of rapid cycle performance decay, large material capacity loss, structural changes, etc. performance effect
- Summary
- Abstract
- Description
- Claims
- Application Information
AI Technical Summary
Problems solved by technology
Method used
Image
Examples
Embodiment 1
[0025] Put the metal salt or metal hydroxide and the positive electrode material of lithium ion battery into a conventional amount of organic solvent for mechanical mixing treatment, pretreatment at low temperature, and then roasting at high temperature to synthesize M y o z ·LiCoO 2 (M y o z ·LiNi x co 1-x o 2 ) Lithium-ion battery positive electrode material; the ratio of metal salt or metal hydroxide to the positive electrode material is measured and dosed according to the molar ratio of 0.01 to 0.05; the specific steps are as follows: aluminum isopropoxide and LiCoO 2 Weighing is carried out according to the molar ratio of 0.1:100. First, the aluminum salt is added to a conventional amount of citric acid, and the ethylene glycol solution is stirred at 90 ° C. At the same time, the LiCoO 2 Slowly add to the solution until it becomes a gel. The mixture of gel, acetone and ethanol (1:1) was ball-milled in a stainless steel ball mill tank for 4 hours according to the ma...
Embodiment 2
[0028] Magnesium acetate and LiCoO 2 Weigh according to the molar ratio of 0.01:100. Magnesium acetate was added to the mixed solution of citric acid and ethylene glycol and stirred at 85°C, while the LiCoO 2 Slowly add to the solution until it becomes a gel. Gel and acetone were ball-milled in an agate ball mill jar for 8 hours according to the mass ratio of 10:1, and the gel after ball-milling was vacuum-dried at 100°C for 3 hours, then calcined at 500°C for 8 hours, and cooled in a furnace to obtain 0.01MgO ·LiCoO 2 Cathode material. The composite material was taken out, and its phase structure was analyzed, from image 3 It can be seen that the crystal structure of the material has not changed, and the layered structure is still maintained. The electrochemically active assembly conditions and test conditions of the sample are consistent with Example 1, and the cycle capacity test curve is shown in Figure 4 .
Embodiment 3
[0030] Aluminum hydroxide and LiNi 0.8 co 0.2 o 2 Weigh according to the molar ratio of 0.04:100. Add aluminum hydroxide to citric acid and ethylene glycol solution and stir at 80°C, while LiNi 0.8 co 0.2 o 2Slowly add to the solution until it becomes a gel. The mixture of gel, acetone and ethanol (4:1) was ball milled in a stainless steel ball mill jar for 6 hours according to the mass ratio of 10:1, and the gel after ball milling was vacuum-dried at 100°C for 1 hour, and then baked at 600°C for 12 hours Afterwards, cooling with the furnace was carried out to obtain 0.02Al 2 o 3 ·LiNi 0.8 co 0.2 o 2 Cathode material. The composite material was taken out, and its phase structure was analyzed, from Figure 5 It can be seen that the crystal structure of the material has not changed, and the layered structure is still maintained. The electrochemically active assembly conditions and test conditions of the sample are consistent with Example 1, and the cycle capacity te...
PUM
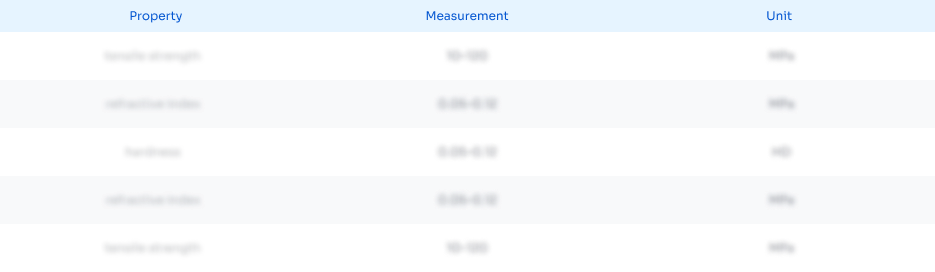
Abstract
Description
Claims
Application Information

- Generate Ideas
- Intellectual Property
- Life Sciences
- Materials
- Tech Scout
- Unparalleled Data Quality
- Higher Quality Content
- 60% Fewer Hallucinations
Browse by: Latest US Patents, China's latest patents, Technical Efficacy Thesaurus, Application Domain, Technology Topic, Popular Technical Reports.
© 2025 PatSnap. All rights reserved.Legal|Privacy policy|Modern Slavery Act Transparency Statement|Sitemap|About US| Contact US: help@patsnap.com