Bulk phase-doped modified lithium ion battery positive electrode material and its preparation method
A technology for lithium ion batteries and cathode materials, which is applied in battery electrodes, chemical instruments and methods, circuits, etc., can solve the problems of reducing specific energy density, reducing material bulk density, etc., and achieves lower synthesis temperature, simple preparation process, and environmental friendliness. Effect
- Summary
- Abstract
- Description
- Claims
- Application Information
AI Technical Summary
Problems solved by technology
Method used
Image
Examples
Embodiment 1
[0016] Put 0.25 moles of lithium carbonate, 0.475 moles of ferrous oxalate dihydrate, 0.025 moles of titanium dioxide and 0.5 moles of ammonium dihydrogen phosphate in an agate mortar and mix evenly, add an appropriate amount of distilled water, and grind it until the rheological phase, at 100 ℃ for 12 hours to obtain a precursor; move the precursor into a high-temperature furnace, and under the protection of nitrogen, raise the temperature to 400°C at a rate of 2°C / min, keep the temperature for 5 hours, and then lower it to room temperature to obtain a pyrolysis precursor Put the obtained pyrolysis precursor in an agate mortar, add ethanol and grind until rheological state, raise the temperature to 750°C at a rate of 2°C / min, keep the temperature for 20 hours, and then lower it to room temperature to obtain LiFe 0.95 Ti 0.05 PO 4 Material. The first discharge capacity of the assembled battery is 143mAhg -1 , The discharge platform voltage is 3.40V, and the capacity retenti...
Embodiment 2
[0018] Put 0.5 mole of lithium hydroxide monohydrate, 0.475 mole of ferrous oxalate dihydrate, 0.025 mole of magnesium oxide and 0.5 mole of ammonium dihydrogen phosphate in an agate mortar and mix evenly, add an appropriate amount of ethanol, and grind it until it flows Change the phase and keep the temperature at 60°C for 1 hour to obtain the precursor; move the precursor into a high-temperature furnace, and under the protection of nitrogen, raise the temperature to 400°C at a rate of 2°C / min, keep the temperature for 5 hours, and then lower it to room temperature to prepare Obtain the pyrolysis precursor; put the obtained pyrolysis precursor in an agate mortar, add ethanol and grind until rheological state, raise the temperature to 700°C at a rate of 2°C / min, keep the temperature for 20 hours, and then lower it to room temperature to obtain LiFe 0.95 Mg 0.05 PO 4 Material. The first discharge capacity of the assembled battery is 141mAhg -1 , the discharge platform voltag...
Embodiment 3
[0020] Put 0.5 mole of lithium acetate dihydrate, 0.485 mole of ferrous oxalate dihydrate, 0.015 mole of zinc oxide and 0.5 mole of diammonium hydrogen phosphate in an agate mortar and mix evenly, add an appropriate amount of ethanol, and grind it until the rheological phase , at 60°C for 1 hour to obtain a precursor; move the precursor into a high-temperature furnace, under the protection of nitrogen, raise the temperature to 400°C at a rate of 2°C / min, keep the temperature for 5 hours, and then lower it to room temperature to obtain Pyrolysis precursor; put the obtained pyrolysis precursor in an agate mortar, add ethanol and grind until rheological state, raise the temperature to 700°C at a rate of 2°C / min, keep the temperature for 20 hours, and then lower it to room temperature to obtain LiFe 0.97 Zn 0.03 PO 4 Material. The first discharge capacity of the assembled battery is 138mAhg -1 , the discharge platform voltage is 3.39V, and the capacity retention rate of the bat...
PUM
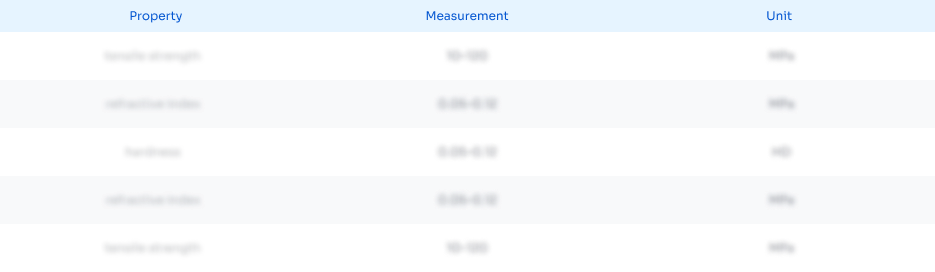
Abstract
Description
Claims
Application Information

- R&D
- Intellectual Property
- Life Sciences
- Materials
- Tech Scout
- Unparalleled Data Quality
- Higher Quality Content
- 60% Fewer Hallucinations
Browse by: Latest US Patents, China's latest patents, Technical Efficacy Thesaurus, Application Domain, Technology Topic, Popular Technical Reports.
© 2025 PatSnap. All rights reserved.Legal|Privacy policy|Modern Slavery Act Transparency Statement|Sitemap|About US| Contact US: help@patsnap.com