High elasticity and high strengh steel and its producing method
A technology of high-strength steel and manufacturing method, applied in the field of high-elasticity, high-strength steel and its manufacturing, can solve the problems of easy cracking, high price, enhanced self-hardening and the like
- Summary
- Abstract
- Description
- Claims
- Application Information
AI Technical Summary
Problems solved by technology
Method used
Image
Examples
Embodiment
[0074] Table 1 shows the chemical composition of the invention steel of the present invention and the conventional steel of the prior art.
[0075] Invention steels A, B, C, D, E, and F are molten steels obtained by mixing and melting pure iron and scrap iron in a 60-ton electric furnace, refining and vacuum degassing, while invention steels G, H, I, J, K, L, M, N, O, P, Q Melt pure iron and scrap iron in a 3-ton electric furnace and refine them to obtain molten steel.
[0076] Inventive steels B, C, G, L, M, and N contain: 0.26-0.36% by weight of C, 1.6-2.2% by weight of Si, 0.5-1.0% by weight of Mn, 1.4-2.4% by weight of Cr, 0.01- 0.05% by weight of Ni, 0.01-0.4% by weight of Mo, 0.005-0.04% by weight of Al, 0.05-0.1% by weight of V, 0.0025-0.02% by weight of N, 0.01-0.1% by weight of Nb, 0.0005-0.01% by weight % Ca, the remainder being Fe and unavoidable impurities.
[0077] Invention steels A and E are made of molten steel with the above components and composition ranges...
PUM
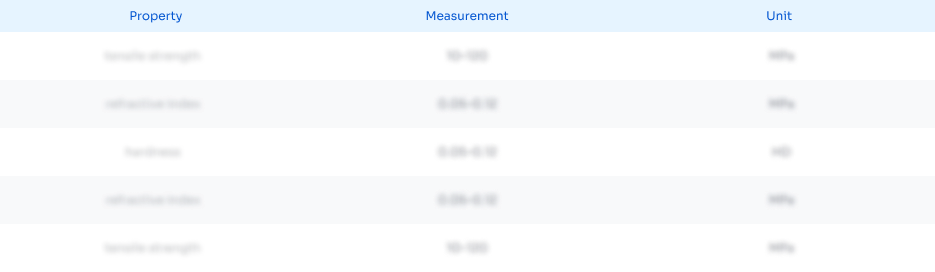
Abstract
Description
Claims
Application Information

- R&D
- Intellectual Property
- Life Sciences
- Materials
- Tech Scout
- Unparalleled Data Quality
- Higher Quality Content
- 60% Fewer Hallucinations
Browse by: Latest US Patents, China's latest patents, Technical Efficacy Thesaurus, Application Domain, Technology Topic, Popular Technical Reports.
© 2025 PatSnap. All rights reserved.Legal|Privacy policy|Modern Slavery Act Transparency Statement|Sitemap|About US| Contact US: help@patsnap.com