Production process of composite steel pipe with cermet lining
A cermet, composite steel pipe technology, applied in the field of steel surface coating, can solve the problems of poor corrosion resistance, high hardness, poor toughness, etc., and achieve the effects of wide application, adjustable composition, and increased reaction temperature
- Summary
- Abstract
- Description
- Claims
- Application Information
AI Technical Summary
Problems solved by technology
Method used
Examples
Embodiment 1
[0016] Example 1: Fe 2 o 3 Al powder 320g, Al powder 108g mix evenly, as the raw material powder for forming the bonding phase. WO 3 Powder 464g, Al powder 54g, graphite powder 24g mix uniformly, as the raw material powder that generates hard ceramic phase. Mix the above powders evenly, preheat to 100°C, and put them into the mother tube. The mother pipe is a Ф74mm carbon steel pipe with a wall thickness of 4mm and a length of 200mm. The steel pipe is installed and stuck on the centrifuge, and the centrifuge is started at a speed of 1110 rpm (the centrifugal acceleration of the reaction raw material is 500m / s 2 ), ignite the material with a tungsten wire, a combustion reaction occurs under centrifugal force, and a huge amount of heat is released. After cooling, the aluminum oxide layer on the surface is removed to obtain a cermet with iron as the binder phase and tungsten carbide as the hard phase. Lined steel pipe.
Embodiment 2
[0017] Example 2: 333g of NiO powder and 81g of Al powder were uniformly mixed as the raw material powder for forming the binder phase. TiC powder 50g, as the raw material powder of hard ceramic phase. Mix the above-mentioned raw material powders evenly, preheat at 100°C, and rotate at 3600 rpm (the centrifugal acceleration of the reaction raw materials is 4975m / s 2 ). The remaining steps are the same as Example 1, and a cermet-lined steel pipe with TiC as the hard phase and Ni as the binding phase can be produced.
Embodiment 3
[0018] Example 3: Fe 2 o 3 Al powder 320g, Al powder 108g mix evenly, as the raw material powder for forming the bonding phase. TiO 2 160g, Al powder 144g, graphite powder 24g as the raw material powder that generates hard ceramic phase. Mix the above-mentioned raw material powders evenly, preheat at 350°C, and rotate at 2700 rpm (the centrifugal acceleration of the reaction raw materials is 2934m / s 2 ), the remaining steps are the same as in Example 1, and can be made into a cermet-lined steel pipe with TiC as the hard phase and Fe as the binder phase.
PUM
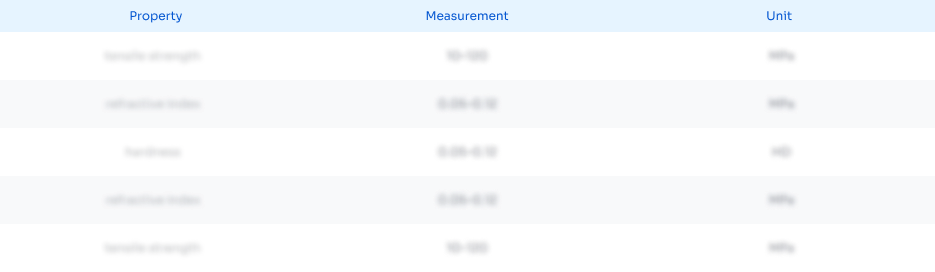
Abstract
Description
Claims
Application Information

- R&D Engineer
- R&D Manager
- IP Professional
- Industry Leading Data Capabilities
- Powerful AI technology
- Patent DNA Extraction
Browse by: Latest US Patents, China's latest patents, Technical Efficacy Thesaurus, Application Domain, Technology Topic, Popular Technical Reports.
© 2024 PatSnap. All rights reserved.Legal|Privacy policy|Modern Slavery Act Transparency Statement|Sitemap|About US| Contact US: help@patsnap.com