Recemizing method for alpha-aminoalcohol compounds and its catalyst
A technology of amino alcohols and composite catalysts, which is applied in the preparation of amino hydroxyl compounds, the preparation of organic compounds, and physical/chemical process catalysts. Difficulty and other issues
- Summary
- Abstract
- Description
- Claims
- Application Information
AI Technical Summary
Problems solved by technology
Method used
Image
Examples
example 1
[0014] Example 1: Catalyst prepared by impregnation
[0015] Heat and dissolve 80g of cobalt nitrate in 140ml of deionized water, add 100g of γ-Al 2 o 3 (Small balls with a diameter of 2-3mm), stirred evenly, soaked overnight, dried in a drying oven at 110°C for 10h, roasted in a muffle furnace at 550°C for 5h, and reduced with hydrogen at 400°C and 2.0Mpa for 2h to obtain the desired product The catalyst is composed of 20.9% cobalt and 86.1% Al2O3.
example 2
[0016] Example 2: Catalyst prepared by co-precipitation method
[0017] Dissolve 50g molybdenum nitrate, 80g cobalt nitrate, 55g chromium nitrate in 750ml deionized water, add 100g Al 2 o 3 powder, stir evenly, heat to 80°C, keep the temperature stable at 80°C and add Na 2 CO 3 Aqueous solution to pH=6.5, let stand, filter, wash to free of Na + Ionization, extrusion molding, drying in a drying oven at 110°C overnight, roasting in a muffle furnace at 550°C for 5 hours, and reducing with hydrogen at 400°C and 2.0Mpa for 2 hours to obtain the desired catalyst. The composition of the catalyst is molybdenum 8.0 %, Cobalt 12.1%, Chromium 5.3%, Al 2 o 3 74.6%.
example 3
[0018] Example 3: Catalyst prepared by kneading and extruding
[0019] Heat 50g of nickel nitrate, 80g of cobalt nitrate, and 60g of chromium nitrate in 150Ml deionized water, add 100g of γ-Al 2 o 3 Powder, fully ground until completely mixed evenly, extruded, dried overnight in a drying oven at 110°C, roasted in a muffle furnace at 550°C for 5 hours, and reduced with hydrogen at 400°C and 2.0Mpa for 2 hours to obtain the desired catalyst. The composition of the catalyst is 7.5% nickel, 12.0% cobalt, 5.8% chromium, Al 2 o 3 74.7%.
PUM
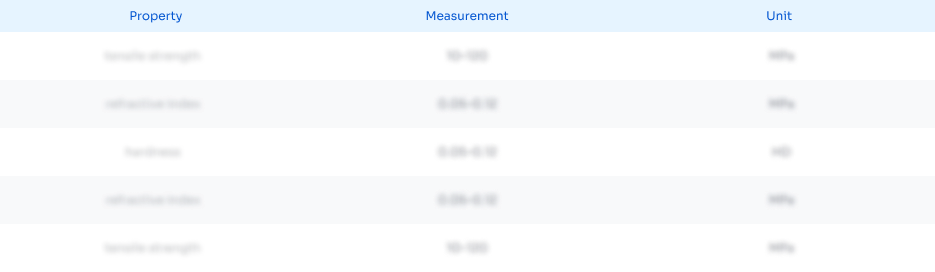
Abstract
Description
Claims
Application Information

- R&D Engineer
- R&D Manager
- IP Professional
- Industry Leading Data Capabilities
- Powerful AI technology
- Patent DNA Extraction
Browse by: Latest US Patents, China's latest patents, Technical Efficacy Thesaurus, Application Domain, Technology Topic, Popular Technical Reports.
© 2024 PatSnap. All rights reserved.Legal|Privacy policy|Modern Slavery Act Transparency Statement|Sitemap|About US| Contact US: help@patsnap.com