Vacuum pressure casting machine for magnesium alloy
A vacuum pressure casting and vacuum pressure technology, which is applied in the field of casting equipment for high-quality magnesium alloy castings, can solve the problems of time-consuming, low productivity, unsafe production process, etc., and achieve stable process parameters, light oxidation degree, and good feeding effect Effect
- Summary
- Abstract
- Description
- Claims
- Application Information
AI Technical Summary
Problems solved by technology
Method used
Image
Examples
Embodiment Construction
[0022] The shell of the magnesium alloy vacuum die casting machine is welded with low-carbon steel plates. It is designed, manufactured, installed, debugged and inspected according to the technical specifications of the pressure vessel, and the low-vacuum seal is guaranteed.
[0023] The compressed gas used in the magnesium alloy vacuum pressure casting machine is dry compressed carbon dioxide gas, and the protective gas is sulfur hexafluoride. Strong exothermic reaction causing accident.
[0024] Magnesium alloy vacuum pressure casting machine is especially suitable for manufacturing cylindrical and large-size magnesium alloy shell castings. Generally, the shape is complex, the thinnest wall is 2mm, and the dimensional accuracy and density are required to be high. Several main parameters of the magnesium alloy vacuum pressure casting machine: filling the mold firstly evacuates the vacuum pressure sealing chamber to less than 10 5 Pa, the magnesium alloy liquid fills the cast...
PUM
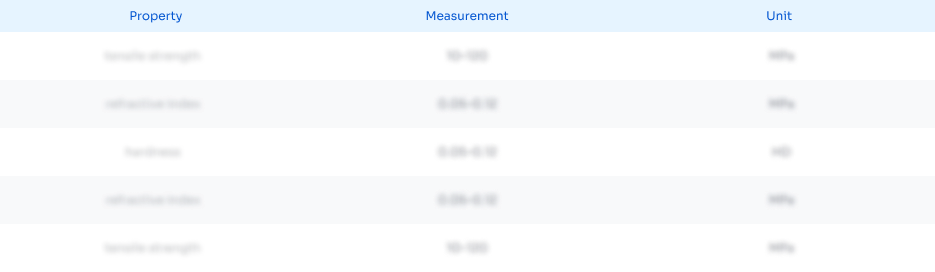
Abstract
Description
Claims
Application Information

- R&D
- Intellectual Property
- Life Sciences
- Materials
- Tech Scout
- Unparalleled Data Quality
- Higher Quality Content
- 60% Fewer Hallucinations
Browse by: Latest US Patents, China's latest patents, Technical Efficacy Thesaurus, Application Domain, Technology Topic, Popular Technical Reports.
© 2025 PatSnap. All rights reserved.Legal|Privacy policy|Modern Slavery Act Transparency Statement|Sitemap|About US| Contact US: help@patsnap.com