Flyash cement auxiliary material and its use
A technology of fly ash cement and auxiliary materials, applied in cement production, sustainable waste treatment, solid waste management, etc., can solve problems affecting cement performance and achieve the effect of solving the three wastes
- Summary
- Abstract
- Description
- Claims
- Application Information
AI Technical Summary
Problems solved by technology
Method used
Examples
Embodiment 1
[0046] Batching of the present invention is as follows: % by weight
[0047] Slag 30
[0048] lime or quicklime 30
[0049] Soot 35
[0050] plaster 5.
[0051] The slag can be slag produced by iron or alloy smelting.
[0052] Coal ash may also include cinders.
[0053] Ca from lime or quicklime ++ or (OH) - The ions act on the slag to form hydrates such as silicon hydrate and calcium aluminate hydrate.
[0054] The amount of gypsum depends on the setting time.
[0055] The above-mentioned raw materials are stacked in layers according to the proportion, and the order is as follows:
[0056] Smelting slag - quicklime - coal ash - gypsum. Crushed and stacked for 1-2 days, the product is ready.
Embodiment 2
[0058] Batching of the present invention is as follows:
[0059] Soot 30
[0060] Slag 35
[0061] Gypsum 3.5
[0062] quicklime 30
[0065] Sodium silicate (also available sodium borate), sodium hydroxide can stimulate the compatibility in slag, coal ash, make 80% noncompatibility glass beads wherein, become effective compound. When stacking, it can be stacked on top of plaster.
[0066] Production technology is identical with embodiment 1.
[0067] The product quality chemical analysis is as follows:
[0068] Lass 13.5 Sio3 22.1 fe2o3 8.2
[0069] Alo 1.82 Cao 42.5 Mgo 4.12
[0070] ∑ 84.15
[0071] Physical analysis:
[0072] Initial setting time 18 Final setting time 34
[0073] Flexural strength 1.8 Compressive strength 22
Embodiment 3
[0075] Product of the present invention is produced cement by following proportioning:
[0076] The present invention: Portland cement clinker=60:40.
[0077]The cement clinker of the present invention with a label above 525 is directly ground, and the fineness requirement is ≤10.0. The compressive strength of the produced cement is 33.8 in 3 days, and the flexural strength is 5.8. Its strength has reached the high label 425. cement.
PUM
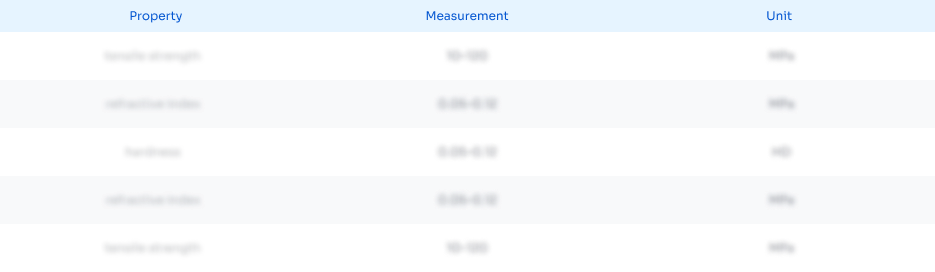
Abstract
Description
Claims
Application Information

- Generate Ideas
- Intellectual Property
- Life Sciences
- Materials
- Tech Scout
- Unparalleled Data Quality
- Higher Quality Content
- 60% Fewer Hallucinations
Browse by: Latest US Patents, China's latest patents, Technical Efficacy Thesaurus, Application Domain, Technology Topic, Popular Technical Reports.
© 2025 PatSnap. All rights reserved.Legal|Privacy policy|Modern Slavery Act Transparency Statement|Sitemap|About US| Contact US: help@patsnap.com