Preparation of chromium anhydride
A technology of chromic anhydride and concentrated sulfuric acid, applied in the direction of chromium oxide/hydrate, etc., can solve the problems of uneven product quality, affecting quality, reducing yield, etc., and achieve the effects of high product purity, increased yield, and good fluidity
- Summary
- Abstract
- Description
- Claims
- Application Information
AI Technical Summary
Problems solved by technology
Method used
Examples
Embodiment 1
[0012] Embodiment 1: earlier the concentrated sulfuric acid that concentration is 95% and concentration are that 70% red alum sodium solution joins in the reactor by 2.2 molar ratio, is that 170V and slow speed stirring are mixed reaction 2 hours at heating voltage, behind the vacuum state Evaporate under reduced pressure (control the evaporation temperature at 120°C) until most of the chromic anhydride crystals are precipitated, then use a centrifuge to dry at a temperature of 85°C, and wash the filter cake with a nearly saturated chromic anhydride solution at a temperature of 87°C , and finally dried at 102°C for 3 hours, and packaged after natural cooling.
Embodiment 2
[0013] Embodiment 2: earlier the concentrated sulfuric acid that concentration is 96% and concentration are that 72% red alum sodium solution joins in the reactor by 2.1 molar ratio, is 170V and mixed reaction 3 hours under stirring at a slow speed at heating voltage, behind the vacuum state Evaporate under reduced pressure (control the evaporation temperature to be 110°C) until most of the chromic anhydride crystals are precipitated, then use a centrifuge to dry at a temperature of 90°C, and the filter cake is washed with a chromic anhydride solution with a saturated temperature of 92°C. Finally, dry at 105°C for 2 hours, and pack after natural cooling.
[0014] In embodiment 1 and embodiment 2, the CI produced by evaporation under reduced pressure 2 , HCI, C r o 2 CI 2 The gas is sent to alkaline water for absorption, and the chromium-containing NaHSO thrown off by the centrifuge 4 The filtrate is directly used for neutralization or acidification, and the washing liquid ...
PUM
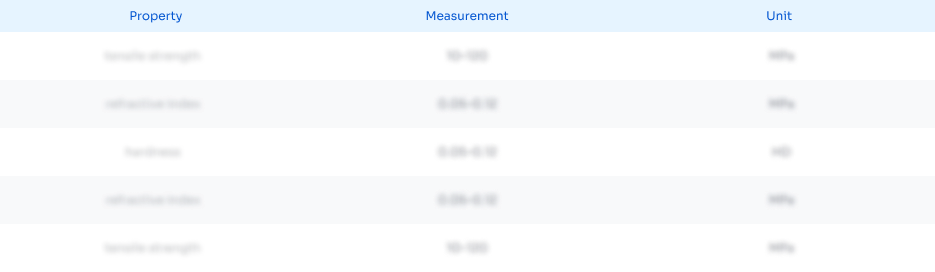
Abstract
Description
Claims
Application Information

- Generate Ideas
- Intellectual Property
- Life Sciences
- Materials
- Tech Scout
- Unparalleled Data Quality
- Higher Quality Content
- 60% Fewer Hallucinations
Browse by: Latest US Patents, China's latest patents, Technical Efficacy Thesaurus, Application Domain, Technology Topic, Popular Technical Reports.
© 2025 PatSnap. All rights reserved.Legal|Privacy policy|Modern Slavery Act Transparency Statement|Sitemap|About US| Contact US: help@patsnap.com