Mechanical zinc-plating process
A mechanical galvanizing and process technology, applied in the direction of pressure inorganic powder coating, etc., can solve the problem of limited corrosion resistance of the coating
- Summary
- Abstract
- Description
- Claims
- Application Information
AI Technical Summary
Problems solved by technology
Method used
Examples
Embodiment 2
[0019] Choose 50 kilograms of cement nails to be plated workpiece Φ3 ~ 6.
[0020] After cleaning the surface of cement nails, put them into the plating barrel; add 70 kg of glass microspheres into the plating barrel, the particle diameters of which include 0.3-0.4 mm, 0.4-0.5 mm, and 0.5-0.6 mm, and the weight ratio is 1:1:1; add water to make it soak the workpiece and microbeads; rotate the plating barrel, and add 500 ml of activated and dispersed plating flux and 5 kg of zinc powder in 5 times during the rotation, with an interval of 5 minutes each time After the feeding is completed, continue to rotate the plating barrel for 10 minutes, pour out the workpiece and glass beads in the plating barrel, separate, and dry to obtain the plated workpiece. The thickness of the coating is 35 to 40 microns.
PUM
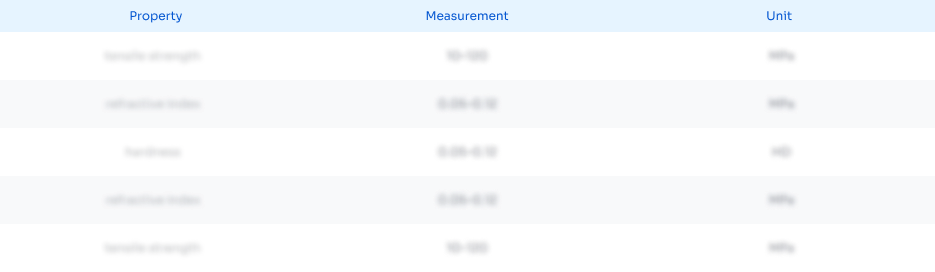
Abstract
Description
Claims
Application Information

- R&D
- Intellectual Property
- Life Sciences
- Materials
- Tech Scout
- Unparalleled Data Quality
- Higher Quality Content
- 60% Fewer Hallucinations
Browse by: Latest US Patents, China's latest patents, Technical Efficacy Thesaurus, Application Domain, Technology Topic, Popular Technical Reports.
© 2025 PatSnap. All rights reserved.Legal|Privacy policy|Modern Slavery Act Transparency Statement|Sitemap|About US| Contact US: help@patsnap.com