Process for refining raw copper bynon-oxidizing nitrogen-doping reducing pyrometallurgy
A pyro-refining, non-oxidizing technology, applied in the field of blister copper pyro-refining, can solve the problems of high energy consumption, low production efficiency, long operation period, etc. Effect
- Summary
- Abstract
- Description
- Claims
- Application Information
AI Technical Summary
Problems solved by technology
Method used
Image
Examples
Embodiment 1
[0038] Such as image 3 As shown, the liquid blister copper is put into the rotary anode furnace (10), and after blowing nitrogen into the slag, the waste nitrogen discharged from the oxygen station is transported into the nitrogen tank (3) for storage through the nitrogen compressor (2). When smelting operation, first open the N 2 Adjust the valve (8), reduce the nitrogen gas to 0.35 ~ 0.40Mpa through the pressure reducing valve (4), and use the heater (5) to heat, observe the pressure gauge (6) and flow meter (7), and turn the anode furnace (10) , so that the spray gun (11) is buried at 600-800 mm below the copper liquid surface, and then the regulating valve (1) (1) (valve degree 50%) is opened to make the reducing agent and N 2 Fully mixed in the mixing container (9), then adjust the valve (1) and valve (8) reasonably to the required reducing agent and N 2 flow, so that N 2 / reducing agent=1.0-1.5, carry out the reduction operation to the end.
Embodiment 2
[0040] Such as Figure 4 As shown, when refining blister copper in a rotary anode furnace, in order to more effectively enhance the stirring performance of molten copper and improve the reaction kinetics conditions, several porous plug air bricks (16 ) (2 in this embodiment), so that N 2 + The reducing agent is sprayed into the melt from the bottom of the furnace. And according to the height of the copper liquid level, reasonably control the N 2 pressure.
Embodiment 3
[0042] Such as Figure 5 As shown, when the reflective anode furnace (15) is used, the flow of the reducing agent is adjusted through the regulating valve (1), and the flow rate of the gear flow meter (13) is observed, so that the reducing agent enters the inner cavity of the nozzle (14). Nitrogen is transported to the gas storage tank (3) through the nitrogen compressor (2) for storage. When in use, it is adjusted to a reasonable nitrogen flow value (generally Control is N 2 / reducing agent=1.0-1.3) nitrogen is sent to the outer chamber of the nozzle (14), so that the reducing agent is fully mixed in the mixing chamber at the front end of the nozzle. Due to the high-pressure impact of nitrogen, the reducing agent quickly becomes dispersed and sprayed into the copper liquid in the reverberatory furnace (15) to enter the reduction operation, thereby improving the reduction efficiency.
PUM
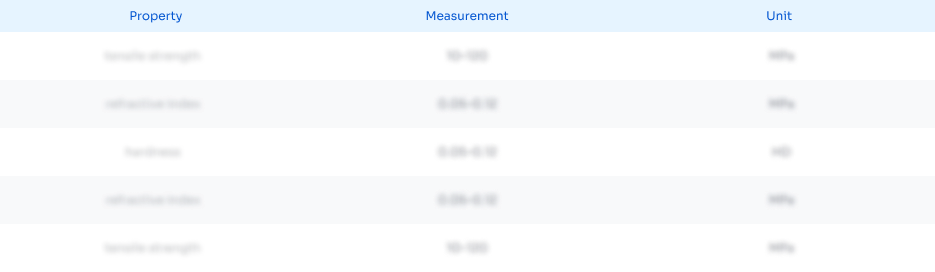
Abstract
Description
Claims
Application Information

- R&D
- Intellectual Property
- Life Sciences
- Materials
- Tech Scout
- Unparalleled Data Quality
- Higher Quality Content
- 60% Fewer Hallucinations
Browse by: Latest US Patents, China's latest patents, Technical Efficacy Thesaurus, Application Domain, Technology Topic, Popular Technical Reports.
© 2025 PatSnap. All rights reserved.Legal|Privacy policy|Modern Slavery Act Transparency Statement|Sitemap|About US| Contact US: help@patsnap.com