Process for preparing flame-retarding phosphorus copolymerized terylene chips
A technology for copolymerizing flame retardant and polyester chips, applied in the polyester chemical field, can solve the problems of affecting the flame retardant effect, decreasing spinnability, and high iron content in chips, achieving uniform and lasting flame retardant effect, easy production and promotion, and spinnability. good effect
- Summary
- Abstract
- Description
- Claims
- Application Information
AI Technical Summary
Problems solved by technology
Method used
Examples
Embodiment 1
[0024] Example 1: Take 100kg of EG and put it into a preparation tank, add 100kg of flame retardant 2-carboxyethylphenylphosphoric acid under stirring, and heat up to 160°C to obtain 50wt% ethylene glycol (EG) preparation solution of flame retardant.
[0025] Take 2000kg of purified terephthalic acid (PTA) and 950kg of ethylene glycol (EG) into the beating tank for beating. After beating evenly, it will be continuously entered into the esterification tank for esterification at 255°C under normal pressure. After the esterification is completed, 440kg will be transferred to the polymerization tank. , add 190kg of the above-mentioned flame retardant preparation solution, precondense in low vacuum at a temperature of 240 to 270° C., and polymerize in a high vacuum (90 Pa) at a temperature of 283° C. to obtain polyester chips. The slice index is shown in Table 1.
Embodiment 2
[0031] Example 2: Get 100kg EG and add it to the preparation tank, add 133kg of flame retardant 2-carboxyethylphenylphosphoric acid (water content 25%) under stirring, heat up to 160°C to obtain ethylene glycol (EG) modulation of 50wt% flame retardant liquid.
[0032] Take 2000kg of purified terephthalic acid (PTA) and 950kg of ethylene glycol (EG) into the beating tank for beating. Kettle, add 190kg of the above-mentioned flame retardant preparation solution, precondense polycondensation at a low vacuum temperature of 240-270°C, and polymerize polyester chips at a high vacuum (90Pa) at a temperature of 284°C.
Embodiment 3
[0033] Example 3: Get 100kg EG and add it to the preparation tank, add 83kg of flame retardant 2-carboxyethylphenylphosphoric acid (water content 25%) under stirring, heat up to 160°C to obtain ethylene glycol (EG) modulation of 40wt% flame retardant liquid.
[0034] Take 2000kg of purified terephthalic acid (PTA) and 950kg of ethylene glycol (EG) into the beating tank for beating. Add 210kg of the above-mentioned flame retardant preparation solution to the kettle, pre-condense in low vacuum at a temperature of 240-270°C, and polymerize in a high vacuum (85Pa) at a temperature of 285°C to obtain polyester chips.
PUM
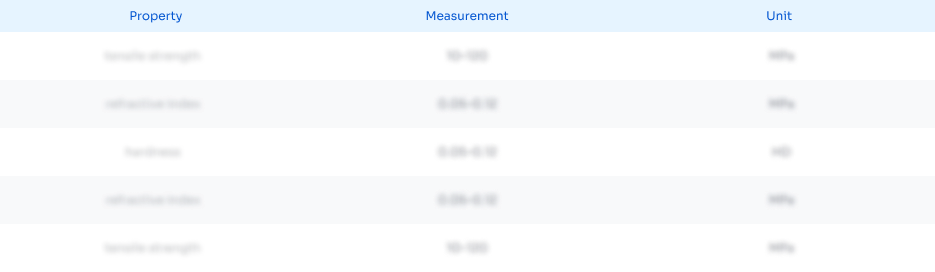
Abstract
Description
Claims
Application Information

- R&D
- Intellectual Property
- Life Sciences
- Materials
- Tech Scout
- Unparalleled Data Quality
- Higher Quality Content
- 60% Fewer Hallucinations
Browse by: Latest US Patents, China's latest patents, Technical Efficacy Thesaurus, Application Domain, Technology Topic, Popular Technical Reports.
© 2025 PatSnap. All rights reserved.Legal|Privacy policy|Modern Slavery Act Transparency Statement|Sitemap|About US| Contact US: help@patsnap.com