Impellers (rotor)of Root's blower manufacturing method
A technology of Roots blower and manufacturing method, which is applied in the direction of mechanical equipment, machine/engine, liquid fuel engine, etc., can solve problems such as complicated production process, and achieve the effects of saving energy consumption, low casting temperature, and reducing air volume loss
- Summary
- Abstract
- Description
- Claims
- Application Information
AI Technical Summary
Problems solved by technology
Method used
Image
Examples
Embodiment Construction
[0018] Its manufacturing method is:
[0019] Preheat the upper and lower templates 3 and 1 of the mold, the cavity mold 2, and the core to 180-200°C, apply a release agent after heating, and then fix the cavity mold 2 on the lower template 1 first, install Insert the core, cover the upper template 3, fix the pouring sleeve, pour the alloy smelted according to the general method into the mold, the casting temperature is 450°C, open the mold after hardening and take out the finished product, the casting is quenched at 180°C and placed at room temperature for 48 Available in hours.
[0020] After the mold is opened, the mold is coated with a release agent, the mold is closed for secondary casting, and the mold does not need to be reheated.
[0021] In the above method, the release agent is water glass plus talcum powder to prepare gruel.
[0022] Shown in Fig. 1, 2, 3 is this Roots blower impeller (rotor) production mold. The details are as follows:
[0023] This Roots...
PUM
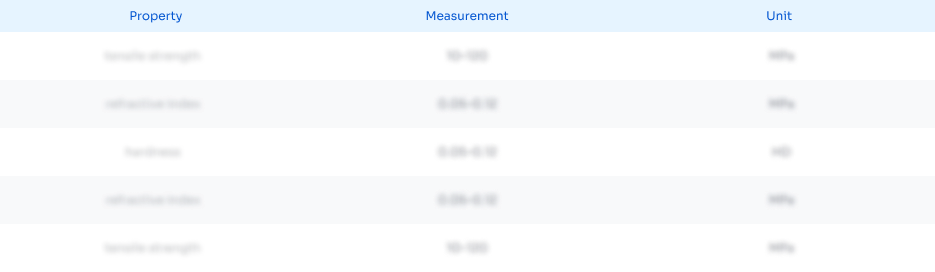
Abstract
Description
Claims
Application Information

- R&D
- Intellectual Property
- Life Sciences
- Materials
- Tech Scout
- Unparalleled Data Quality
- Higher Quality Content
- 60% Fewer Hallucinations
Browse by: Latest US Patents, China's latest patents, Technical Efficacy Thesaurus, Application Domain, Technology Topic, Popular Technical Reports.
© 2025 PatSnap. All rights reserved.Legal|Privacy policy|Modern Slavery Act Transparency Statement|Sitemap|About US| Contact US: help@patsnap.com