Process for producing alkylidene dibasic alcohol
A technology of alkylene glycol and alkylene oxide, which is applied in the field of preparation of alkylene glycol, can solve the problems of short catalyst life, poor heat resistance, etc., achieve low conversion rate, good thermal stability, selectivity The effect of improving performance and yield
- Summary
- Abstract
- Description
- Claims
- Application Information
AI Technical Summary
Problems solved by technology
Method used
Examples
preparation example Construction
[0040] Preparation method of composite resin
[0041] 【Example】
[0042] In a 500 ml three-necked bottle, add 200 ml of distilled water and 0.9 g of gelatin, start stirring and raise the temperature to completely dissolve the polyvinyl alcohol. Stop stirring, add monomer mixture solution (29.2 gram styrene, 5.8 gram divinylbenzene (40% by weight), 1.2 gram carbon nanotube, 35.6 gram 200 # Gasoline, 0.35 g of benzoyl peroxide), start stirring, heat up to 85°C, and react for 4 hours. The temperature was raised to 95°C for about 2 hours. After the reaction, pour out the upper liquid, wash with 85°C hot water for several times, and then wash with cold water for several times, then filter, dry, and weigh to obtain composite beads. Functionalization of composite beads: Add 20.6 grams of composite beads A and 80 milliliters of chloromethyl ether into a 500-ml three-necked bottle, start stirring and heat up to 30°C, add 8 grams of zinc chloride as a catalyst, and heat up to 39-40°C...
Embodiment 1~5
[0055] 15 milliliters of each of the above-mentioned catalysts A, B, C, D, and E (grain size 20-40 mesh) were packed in a stainless steel fixed-bed reactor with a diameter of 10 mm and a length of 350 mm respectively, and the raw material water and ethylene oxide Alkanes are fed with a metering pump at a molar ratio of 12:1. The pressure of the reaction system is 1.2 MPa, the reaction temperature is 90°C, and the liquid space velocity is 3 hours -1 , The product was qualitatively and quantitatively analyzed by HP5890 gas chromatography, and the results are listed in Table 1.
Embodiment 6
[0059] 15 milliliters of the catalyst C (particle size 20-40 mesh) is packed in a stainless steel fixed-bed reactor with a diameter of 10 mm and a length of 350 mm, and feed water and ethylene oxide with a metering pump at a molar ratio of 22:1. . The pressure of the reaction system is 1.2 MPa, the reaction temperature is 90°C, and the liquid space velocity is 6 hours -1 , The product was qualitatively and quantitatively analyzed by HP5890 gas chromatography, and the results are listed in Table 1.
PUM
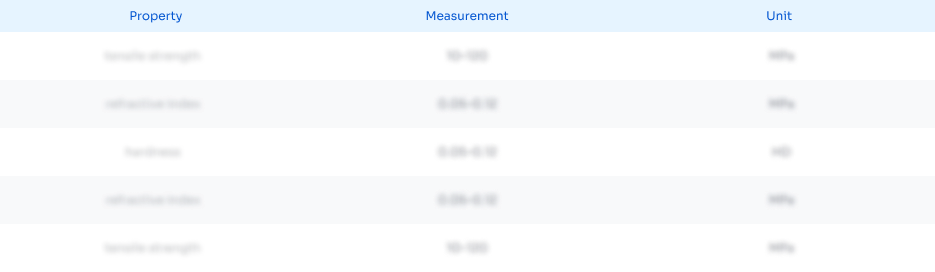
Abstract
Description
Claims
Application Information

- R&D
- Intellectual Property
- Life Sciences
- Materials
- Tech Scout
- Unparalleled Data Quality
- Higher Quality Content
- 60% Fewer Hallucinations
Browse by: Latest US Patents, China's latest patents, Technical Efficacy Thesaurus, Application Domain, Technology Topic, Popular Technical Reports.
© 2025 PatSnap. All rights reserved.Legal|Privacy policy|Modern Slavery Act Transparency Statement|Sitemap|About US| Contact US: help@patsnap.com