Orgnic electroluminescence device and its preparation method
An electroluminescent device, an organic technology, applied in the direction of electroluminescent light source, electric solid device, semiconductor/solid device manufacturing, etc., can solve the problems of pixel short circuit, large equipment investment, organic film damage, etc., to reduce reflection To suppress the voltage, reduce the production cost, the effect of low lighting voltage
- Summary
- Abstract
- Description
- Claims
- Application Information
AI Technical Summary
Problems solved by technology
Method used
Image
Examples
Embodiment 1
[0050] (The entire preparation process of OLEDs is carried out in the purification workshop). The ITO glass with a sheet resistance of 15Ω is ultrasonically cleaned and dried with acetone-ethanol solution (volume ratio 2:1). The ITO film thickness is 170nm. A group of parallel and separated straight lines with a line width of 400 μm were produced. Then, the first layer of insulation material PI for isolation columns is spin-coated with a film thickness of 2 μm. Lithograph PI into a network structure, that is, there are PI lines in the vertical direction to ITO and the parallel direction to ITO (between the ITO lines), and develop in 3% NaOH solution for 30s, so that the cross-section of the lines forms a positive trapezoid with a small top and a large bottom shape, with a line width of 30 μm. Bake in a convection oven at 210° C. for 30 minutes to completely cure the PI. Then continue to spin-coat the second layer of isolation column insulating material PI on this basis, with...
Embodiment 2
[0052] (The entire preparation process of OLEDs is carried out in the purification workshop). The ITO glass with a sheet resistance of 5Ω is ultrasonically cleaned and dried with acetone-ethanol solution (volume ratio 2:1). The ITO film thickness is 200nm. A group of parallel and separated straight lines with a line width of 200 μm were produced. Then spin-coat the first layer of positive photoresist AZ6112 (Clariant Co., Ltd., Japan) with a film thickness of 0.5 μm. The photolithography forms a network structure, that is, there are positive photoresist lines in the direction perpendicular to the ITO and parallel to the ITO (between the ITO lines), and the positive photoresist developer is used to develop the cross-section of the lines to form a small top and a large bottom. regular trapezoidal shape with a line width of 20 μm. Bake in a convection oven at 220° C. for 30 minutes to completely cure the positive photoresist. Then continue to spin-coat the second layer of isola...
Embodiment 3
[0054](The entire preparation process of OLEDs is carried out in the purification workshop). The ITO glass with a sheet resistance of 15Ω is ultrasonically cleaned and dried with acetone-ethanol solution (volume ratio 2:1). The ITO film thickness is 170nm. A group of parallel and separated straight lines with a line width of 600 μm were produced. Then spin-coat the first layer of isolation column insulating material photosensitive PI with a film thickness of 1 μm. The photosensitive PI is photolithographically formed into a network structure, that is, there are photosensitive PI lines in the direction perpendicular to the ITO and parallel to the ITO (between the ITO lines), and developed in a dimethylformamide developer for 50 seconds to form a cross-section of the lines. A regular trapezoidal shape with a small top and a large bottom, with a line width of 50 μm. Bake in a convection oven at 220° C. for 30 minutes to completely cure the photosensitive PI. On this basis, cont...
PUM
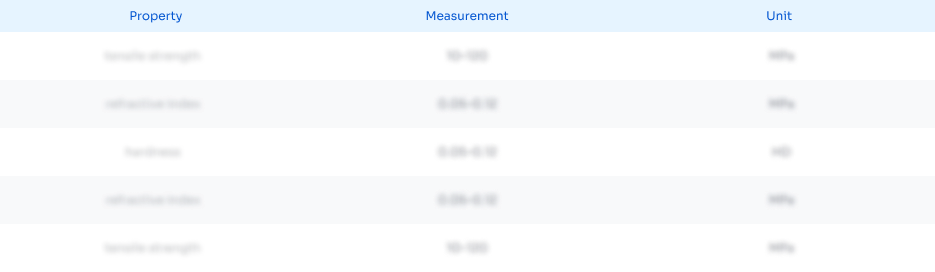
Abstract
Description
Claims
Application Information

- Generate Ideas
- Intellectual Property
- Life Sciences
- Materials
- Tech Scout
- Unparalleled Data Quality
- Higher Quality Content
- 60% Fewer Hallucinations
Browse by: Latest US Patents, China's latest patents, Technical Efficacy Thesaurus, Application Domain, Technology Topic, Popular Technical Reports.
© 2025 PatSnap. All rights reserved.Legal|Privacy policy|Modern Slavery Act Transparency Statement|Sitemap|About US| Contact US: help@patsnap.com