Dispersion resin for cathode electrophoretic coating matched with film pretreatment as well as preparation method and application of dispersion resin
A cathodic electrophoretic coating and dispersing resin technology, applied in the coating field, can solve the problems of poor swimming penetration, weak corrosion resistance, pinholes in galvanized sheets, etc., and achieve good swimming penetration, reduced roughness, and good electric field shielding. Effect
- Summary
- Abstract
- Description
- Claims
- Application Information
AI Technical Summary
Problems solved by technology
Method used
Image
Examples
Embodiment 1
[0048] Example 1: Preparation of Cathodic Electrophoretic Paint A component - emulsion.
[0049] The emulsion is taken from the workshop, and the methods described in the US patents US2010167072A1, US5868820 and US3984299 can also be referred to for details.
[0050]Prepare the following components in parts by weight: 880 parts epoxy resin 828, 2 parts benzylamine catalyst, 260 parts bisphenol A, 180 parts homemade blocked polyester resin, 60 parts methyl isobutyl ketone, 1100 parts blocked Isocyanate crosslinking agent (prepared by the reaction of diphenylmethane diisocyanate with caprolactam, ethylene glycol butyl ether and trimethylolpropane, the molar ratio of caprolactam, ethylene glycol butyl ether and trimethylolpropane is 2:5 : 3, solid content 90%), 60 parts of N-methyl monoethanolamine, 140 parts of ketimine (by dehydration reaction of diethylenetriamine and methyl isobutyl ketone, solid content 70%), 60 parts of propylene glycol methyl ether, 60 parts of ethylene g...
Embodiment 2
[0052] Example 2: Preparation of Dispersion Resin I.
[0053] (1) prepare the following components in parts by weight: 780 parts of glycidyl neodecanoate, 120 parts of diethylenetriamine, 100 parts of propylene glycol methyl ether;
[0054] Under the protection of inert gas, add diethylenetriamine to the reaction vessel with a stirring device and a circulating cooling device, and control the rotating speed of the stirring device to be 100-200 rpm; add glycidyl neodecanoate dropwise, and open the circulating cooling device at the same time, Incubate for 4 hours at a temperature of 100-120°C; add propylene glycol methyl ether and stir evenly to obtain an amino resin containing active hydrogen, which is for later use;
[0055] (2) Prepare the following components in parts by weight: 280 parts of self-made aliphatic epoxy resins (epoxy equivalent: 350-400), 80 parts of bisphenol A, 4 parts of triphenylphosphine, 20 parts of methyl Isobutyl ketone, 50 parts of propylene glycol met...
Embodiment 3
[0058] Example 3: Preparation of Dispersion Resin II.
[0059] The following components were prepared in parts by weight: 280 parts of homemade aliphatic epoxy resin (epoxy equivalent: 350-400), 80 parts of bisphenol A, 4 parts of triphenylphosphine, 20 parts of methyl isobutyl ketone , 50 parts of propylene glycol methyl ether, 250 parts of amino resin containing active hydrogen obtained in the step (1) of Example 2, 96 parts of thiopropylene glycol, 56 parts of dimethylol propionic acid, 300 parts of deionized water
[0060] Under the protection of inert gas, add epoxy resin, bisphenol A, methyl isobutyl ketone to the reaction vessel with heating device and stirring device, heat to 110-120 ℃, and control the rotating speed of the stirring device to be 100-200rpm; Add triphenylphosphine catalyst, keep the temperature between 130-140 ℃ for 1.5 hours, cool down to 70-90 ℃, and keep the temperature for 1-2 hours;
[0061] The amino resin containing active hydrogen obtained in s...
PUM
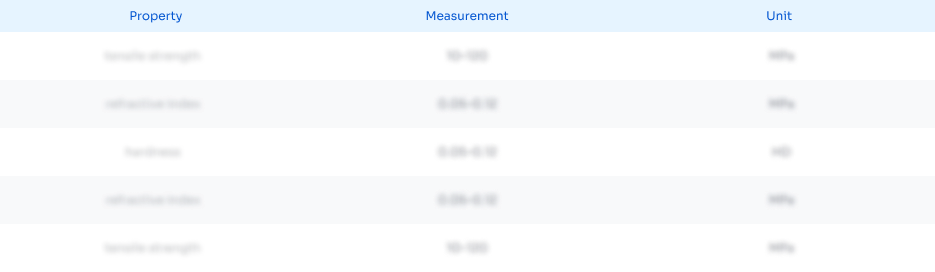
Abstract
Description
Claims
Application Information

- R&D Engineer
- R&D Manager
- IP Professional
- Industry Leading Data Capabilities
- Powerful AI technology
- Patent DNA Extraction
Browse by: Latest US Patents, China's latest patents, Technical Efficacy Thesaurus, Application Domain, Technology Topic, Popular Technical Reports.
© 2024 PatSnap. All rights reserved.Legal|Privacy policy|Modern Slavery Act Transparency Statement|Sitemap|About US| Contact US: help@patsnap.com