Production process of niobium-molybdenum chilled alloy composite roller
A production process and composite roll technology, applied in the field of composite rolls, can solve the problems of composite roll wear resistance, poor hardness, unsatisfactory use effect, large hardness drop, etc., to improve hardenability, increase hardness, and reduce hardness drop Effect
- Summary
- Abstract
- Description
- Claims
- Application Information
AI Technical Summary
Problems solved by technology
Method used
Image
Examples
Embodiment 1
[0071] The production process of the niobium-molybdenum chilled carbide composite roll of the present embodiment comprises the following steps:
[0072] Step 1, prepare working layer raw materials:
[0073] Weigh the following raw materials by weight: C 3.0%, Si 0.8%, Mn 0.5%, Cr 1.0-1.2%, Nb 0.5%, modified Mo 0.6%, Ni 3.0%, modified carbon nanotubes 0.2%, The remainder is Fe;
[0074] Step 2, prepare the raw materials for the core layer:
[0075] C 4.1%, Si 0.5%, Mn 0.15%, P 0.03%, S 0.02%, the balance is Fe;
[0076] Step 3, using a 1.5-ton intermediate frequency furnace to smelt the raw material for the working layer to prepare molten iron for the working layer, and a 3-ton intermediate frequency furnace to smelt the raw material for the core layer to prepare the core roll neck molten iron;
[0077] Step 4: Centrifugally pour molten iron in the working layer at 1350°C, and after the pouring is completed, a working layer is formed;
[0078] In step 5, the heat treatment ...
Embodiment 2
[0098] The production process of the niobium-molybdenum chilled carbide composite roll of the present embodiment comprises the following steps:
[0099] Step 1, prepare working layer raw materials:
[0100] Weigh the following raw materials by weight: C 3.2%, Si 1.0%, Mn 0.6%, Cr 1.2%, Nb 0.6%, modified Mo 0.7%, Ni 3.2%, modified carbon nanotubes 0.7%, the balance is Fe;
[0101] Step 2, prepare the raw materials for the core layer:
[0102] C 4.3%, Si 1.4%, Mn 0.25%, P 0.1%, S 0.04%, the balance is Fe;
[0103] Step 3, using a 1.5-ton intermediate frequency furnace to smelt the raw material for the working layer to prepare molten iron for the working layer, and a 3-ton intermediate frequency furnace to smelt the raw material for the core layer to prepare the core roll neck molten iron;
[0104] Step 4: Centrifugally pour molten iron in the working layer at 1370°C, and after the pouring is completed, a working layer is formed;
[0105] In step 5, the heat treatment process...
Embodiment 3
[0125] The production process of the niobium-molybdenum chilled carbide composite roll of the present embodiment comprises the following steps:
[0126] Step 1, prepare working layer raw materials:
[0127] Weigh the following raw materials by weight: C 3.1%, Si 0.9%, Mn 0.55%, Cr 1.1%, Nb 0.55%, modified Mo 0.65%, Ni 3.1%, modified carbon nanotubes 0.45%, the remainder is Fe;
[0128] Step 2, prepare the raw materials for the core layer:
[0129] C 4.2%, Si 0.9%, Mn 2.0%, P 0.06%, S 0.03%, the balance is Fe;
[0130] Step 3, using a 1.5-ton intermediate frequency furnace to smelt the raw material for the working layer to prepare molten iron for the working layer, and a 3-ton intermediate frequency furnace to smelt the raw material for the core layer to prepare the core roll neck molten iron;
[0131] Step 4: Centrifugally pour the molten iron in the working layer at 1360°C. After the casting is completed, the working layer is formed;
[0132] In step 5, the heat treatment...
PUM
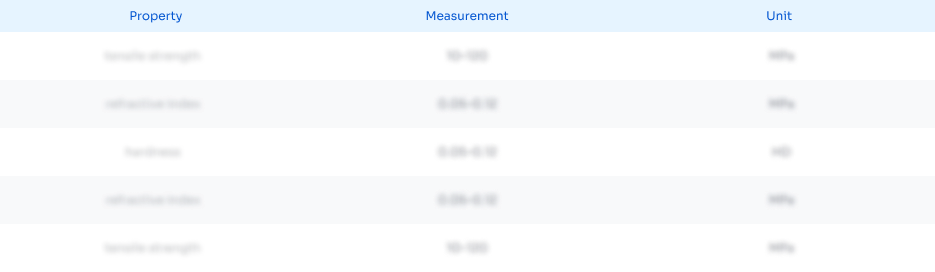
Abstract
Description
Claims
Application Information

- R&D
- Intellectual Property
- Life Sciences
- Materials
- Tech Scout
- Unparalleled Data Quality
- Higher Quality Content
- 60% Fewer Hallucinations
Browse by: Latest US Patents, China's latest patents, Technical Efficacy Thesaurus, Application Domain, Technology Topic, Popular Technical Reports.
© 2025 PatSnap. All rights reserved.Legal|Privacy policy|Modern Slavery Act Transparency Statement|Sitemap|About US| Contact US: help@patsnap.com