Lightweight thermal insulation decoration panel and preparation method thereof
A decorative panel, lightweight technology, used in covering/lining, architecture, building structure, etc., can solve the problems of complex construction process, high system cost, high water absorption, and achieve poor sound insulation performance and low thermal conductivity. , good compatibility
- Summary
- Abstract
- Description
- Claims
- Application Information
AI Technical Summary
Problems solved by technology
Method used
Image
Examples
Embodiment 1
[0027] Step 1, 35 parts of perlite, 5 parts of bentonite, 10 parts of zeolite, 5 parts of kaolin, 5 parts of tuff, 10 parts of black mud, 0.4 parts of green ceramic silica fume, 10 parts of fluorite tailings by mass percentage. After the raw materials are mixed, then crushed, wet ball milled, and evenly aged, then spray-dried, granulated, and pulverized, and pressed into a mold to obtain a green body with notches, and the green body is dried;
[0028] Step 2: Mix 150 parts of cement, 4 parts of microsilica, 130 parts of fly ash, 1 part of hydrophobic component, 0.5 part of water-retaining component, 4 parts of rubber powder, 5 parts of nano-aluminum-magnesium powder, and silica aerosol. 1 part of glue, 1.8 parts of polypropylene fiber, 110 parts of water, 20 parts of hydrogen peroxide, and 1 part of calcium stearate are mixed and poured into the notch of the green body, foamed, molded, hardened and cured;
[0029] Step 3, ball mill to 350 mesh glaze with the raw material of 40...
Embodiment 2
[0031] Step 1, 55 parts of perlite, 10 parts of bentonite, 20 parts of zeolite, 10 parts of kaolin, 15 parts of tuff, 20 parts of black mud, 1.0 parts of green ceramic silica fume, 20 parts of fluorite tailings by mass percentage. After the raw materials are mixed, then crushed, wet ball milled, and evenly aged, then spray-dried, granulated, and pulverized, and pressed into a mold to obtain a green body with notches, and the green body is dried;
[0032] Step 2: Mix 160 parts of cement, 4 parts of microsilica, 130 parts of fly ash, 1 part of hydrophobic component, 0.5 part of water-retaining component, 5 parts of rubber powder, 6 parts of nano-aluminum-magnesium powder, and silica aerosol. 1 part of glue, 1.8 parts of polypropylene fiber, 110 parts of water, 20 parts of hydrogen peroxide, and 1 part of calcium stearate are mixed and poured into the notch of the green body, foamed, molded, hardened and cured;
[0033] Step 3, the raw materials of 60 parts by mass percentage of ...
Embodiment 3
[0035] Step 1, 45 parts of perlite, 6 parts of bentonite, 12 parts of zeolite, 6 parts of kaolin, 8 parts of tuff, 13 parts of black mud, 0.5 parts of green ceramic silica fume, 12 parts of fluorite tailings by mass percentage. After the raw materials are mixed, then crushed, wet ball milled, and evenly aged, then spray-dried, granulated, and pulverized, and pressed into a mold to obtain a green body with notches, and the green body is dried;
[0036] Step 2: Mix 170 parts of cement, 8 parts of microsilica, 130 parts of fly ash, 1 part of hydrophobic component, 0.5 part of water-retaining component, 4 parts of rubber powder, 5 parts of nano-aluminum-magnesium powder, and silica aerosol. 2 parts of glue, 1.8 parts of polypropylene fiber, 110 parts of water, 20 parts of hydrogen peroxide, and 1 part of calcium stearate are mixed and poured into the notch of the green body, foamed, molded, hardened and cured;
[0037] Step 3, the raw materials of 45 parts by mass percentage of ra...
PUM
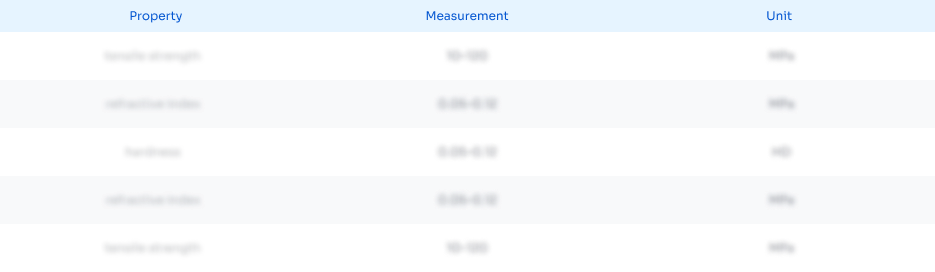
Abstract
Description
Claims
Application Information

- R&D
- Intellectual Property
- Life Sciences
- Materials
- Tech Scout
- Unparalleled Data Quality
- Higher Quality Content
- 60% Fewer Hallucinations
Browse by: Latest US Patents, China's latest patents, Technical Efficacy Thesaurus, Application Domain, Technology Topic, Popular Technical Reports.
© 2025 PatSnap. All rights reserved.Legal|Privacy policy|Modern Slavery Act Transparency Statement|Sitemap|About US| Contact US: help@patsnap.com