Core-shell structure composite powder and preparation method thereof
A technology of composite powder and shell structure, which is applied in metal processing equipment, transportation and packaging, coating, etc., can solve the problems of complex solution chemical reaction and increase the difficulty of operation, and achieve simple process, wide application range and good industrial application prospect Effect
- Summary
- Abstract
- Description
- Claims
- Application Information
AI Technical Summary
Problems solved by technology
Method used
Image
Examples
Embodiment 1
[0036] A core-shell structure composite powder is made of deionized water, metal salts, powder particles, and a gelling agent as raw materials. The amount is 1 to 4 times the total mass of the metal salt and powder particles; the powder particles are one or more of refractory metals and hard materials mixed in any ratio, and the refractory metals are tungsten, molybdenum, tantalum, niobium, zirconium, hafnium , vanadium, chromium, titanium, rhenium, ruthenium or rhodium mixed in any ratio; hard materials are tungsten carbide, molybdenum carbide, titanium carbide, titanium nitride, titanium carbonitride, tantalum carbide, silicon carbide , niobium carbide, titanium boride, tantalum boride, vanadium boride, chromium boride, zirconium boride, tungsten boride, molybdenum boride, niobium boride, aluminium oxide, zirconium oxide, magnesium oxide or beryllium oxide One or more are mixed in any ratio.
[0037] The gelling agent is one or more of polyvinylpyrrolidone, carboxymethylcel...
Embodiment 2
[0040] A preparation method of a core-shell structure composite powder is specifically carried out according to the following steps:
[0041] S1, wetting the insoluble metal salt with deionized water to obtain the wet metal salt, the mass ratio of the deionized water to the metal salt is 0.2 to 2.0, the function is to facilitate the formation of an ice coating layer on the surface of the metal salt in the later stage , too little water cannot form an ice coating structure, and too much water will form hard large ice blocks, which cannot be broken by ball milling.
[0042] The metal salt is a metal carbonate, hydroxycarbonate or oxalate, and the metal is one or more of Co, Ni, Fe, Mn, Cu, Zn or Sn mixed in any ratio; preferably metal Co, One or more of Ni, Fe, and Cu, the metal salts are easily decomposed, and the decomposed products are environmentally friendly.
[0043] S2, freezing the wet metal salt at a freezing temperature of -1 to -18° C. to form an ice coating layer on...
Embodiment 3
[0051] A preparation method of a core-shell structure composite powder is specifically carried out according to the following steps:
[0052] S1, spray 5g of deionized water in the mixture of 28.2g of cobalt carbonate and 4.1g of nickel carbonate to make it wet; the mass ratio of the added mass of deionized water to the metal salt is 0.155;
[0053] S2, freezing the wet cobalt carbonate and nickel carbonate mixture at a temperature of -8°C to form an ice coating layer on the surface of the cobalt carbonate and nickel carbonate to obtain a cobalt carbonate-nickel carbonate-ice solid mixture;
[0054] S3, add the cobalt carbonate-nickel carbonate-ice solid mixture and 2.8 g of liquid nitrogen into the ball milling tank (the amount of liquid nitrogen is 0.075 times the mass of the metal salt-ice solid mixture), and perform ball milling in a low-temperature planetary ball mill at a ball milling speed of 450 r / min, the ball-to-material ratio is 6:1, and the ball milling time is 72...
PUM
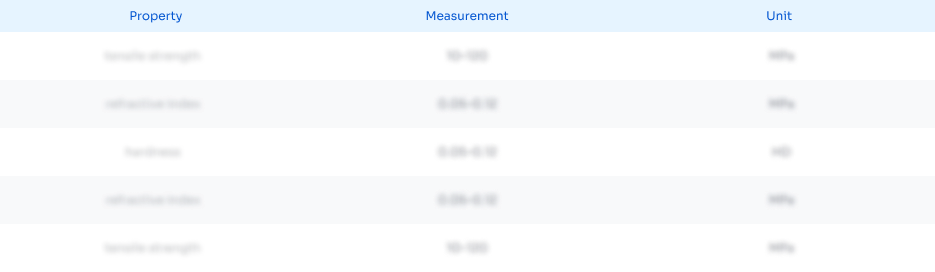
Abstract
Description
Claims
Application Information

- Generate Ideas
- Intellectual Property
- Life Sciences
- Materials
- Tech Scout
- Unparalleled Data Quality
- Higher Quality Content
- 60% Fewer Hallucinations
Browse by: Latest US Patents, China's latest patents, Technical Efficacy Thesaurus, Application Domain, Technology Topic, Popular Technical Reports.
© 2025 PatSnap. All rights reserved.Legal|Privacy policy|Modern Slavery Act Transparency Statement|Sitemap|About US| Contact US: help@patsnap.com