Iron-based catalyst for directly preparing low-carbon olefin from synthesis gas as well as preparation method and application of iron-based catalyst
A technology of iron-based catalysts and low-carbon olefins, which is applied in the direction of catalyst activation/preparation, carbon compound catalysts, catalysts, etc., and can solve the problems of low selectivity of low-carbon olefins and poor catalyst stability
- Summary
- Abstract
- Description
- Claims
- Application Information
AI Technical Summary
Problems solved by technology
Method used
Image
Examples
Embodiment 1
[0062] 1. Preparation of catalyst
[0063] Get 397.1 grams of ferric nitrate, add (1000g) water to dissolve, and obtain material I; Stir and dissolve to obtain material II.
[0064] The materials I and II were stirred and mixed, and 312.5 grams of 40% (weight) aluminum sol material was added under stirring, and then a solution (50 g) containing 0.33 grams of KOH was added, and the pH value of the above slurry was adjusted with ammonia water to make the mixed slurry. pH=6.0, then add a solution (10 g) containing 0.50 g of cerium nitrate, and after thorough stirring, the prepared slurry is formed into microspheres in a spray dryer according to the usual method, and finally the inner diameter is 89 mm and the length is 1700mm In the rotary calcining furnace, calcined at 500 ° C for 2.0 hours, and the prepared catalyst is composed of:
[0065] 50 wt% Fe 100 Mn 60.0 Cu 5.0 Co 1.0 Ga 2.0 K 0.5 Ce 0.5 O x +50 wt% Al 2 O 3
[0066] 2. Reduction, carbonization and evalua...
Embodiment 2
[0080] Take 247.3 grams of ferric nitrate, add (600g) water to dissolve to obtain material I, take 236.1 grams of 50% manganese nitrate, 29.27 grams of copper nitrate, 8.99 grams of gallium nitrate and 35.30 grams of cobalt nitrate in the same container, add (200g) of water, Stir and dissolve to obtain material II.
[0081] The materials I and II were stirred and mixed, and 312.5 grams of 40% (weight) aluminum sol material was added under stirring, and then a KOH solution (50 g) containing 3.28 grams was added, and the acidity of the above-mentioned slurry was adjusted with ammonia water to make the pH of the mixed slurry = 6.0, then add the solution (100g) containing 5.02 grams of cerium nitrate, get the slurry after fully stirring, carry out the microsphere forming of the slurry in the spray dryer, and finally the catalyst made by roasting consists of:
[0082] 50 wt% Fe 100 Mn 110.0 Cu 20.0 Co 20.0 Ga 8.0 K 8.0 Ce 8.0 O x +50 wt% Al 2 O 3
[0083] Reduction of th...
Embodiment 3
[0090] Get 42401 grams of ferric nitrate, add (1000g) water to dissolve, get material I, get 294.5 grams of 50% manganese nitrate, 25.11 grams of copper nitrate, 15.43 grams of gallium nitrate and 30.20 grams of cobalt nitrate in the same container, add (200g) of water, Stir and dissolve to obtain material II.
[0091] The materials I and II were stirred and mixed, and 187.5 grams of 40% (weight) aluminum sol material was added under stirring, and then a solution (100 g) containing 3.52 grams of KOH was added, and the acidity of the above-mentioned slurry was adjusted with ammonia water to make the pH of the mixed slurry. = 6.0, then add a solution (100g) containing 22.60 grams of cerium nitrate, obtain a slurry after thorough stirring, carry out microsphere molding in a spray dryer, and finally the catalyst made by roasting consists of:
[0092] 70wt% Fe 100 Mn 80.0 Cu 10.0 Co 10.0 Ga 8.0 K 5.0 Ce 5.0 O x +30% wt Al 2 O 3
[0093] Reduction of the resulting catalys...
PUM
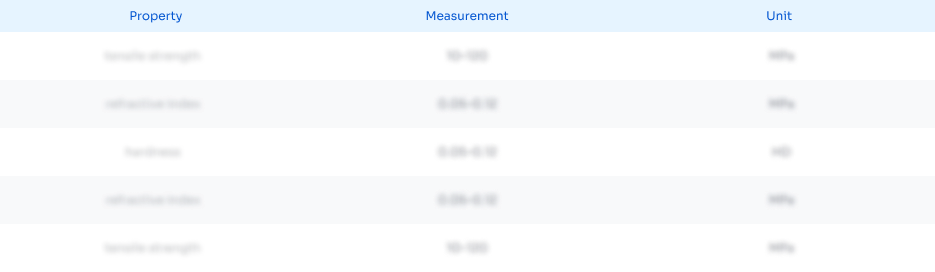
Abstract
Description
Claims
Application Information

- R&D
- Intellectual Property
- Life Sciences
- Materials
- Tech Scout
- Unparalleled Data Quality
- Higher Quality Content
- 60% Fewer Hallucinations
Browse by: Latest US Patents, China's latest patents, Technical Efficacy Thesaurus, Application Domain, Technology Topic, Popular Technical Reports.
© 2025 PatSnap. All rights reserved.Legal|Privacy policy|Modern Slavery Act Transparency Statement|Sitemap|About US| Contact US: help@patsnap.com