Preparation method of foam board with uniform plasmids
A foam board, uniform technology, applied in the field of foam board, can solve the problems of high fragility and breakage rate of packaging board, breakage and damage of packaging board, collision or accidental drop, etc., to improve fragility and damage rate, Effect of improving lubricity and promoting dispersion
- Summary
- Abstract
- Description
- Claims
- Application Information
AI Technical Summary
Problems solved by technology
Method used
Image
Examples
preparation example 1
[0041] The preparation of magnesium hydroxide composite agglomerated particles comprises the following steps:
[0042]Step 1, adding 3kg of nano-silicon dioxide powder and 2kg of nano-titanium dioxide powder to 20kg magnesium nitrate solution to disperse uniformly, the mass concentration of magnesium nitrate solution is 20%, obtain a mixed solution, add ammonia water to the mixed solution, adjust the pH value to 11 , to prepare coated particles with nano-silica powder and nano-titanium dioxide powder as the core, filter and dry them to obtain a solid product;
[0043] In step 2, 1 kg of mica powder and 4 kg of polyethylene glycol are added to the solid product, and spray granulation is carried out to obtain magnesium hydroxide composite agglomerated particles with a particle size of less than 0.1 mm.
preparation example 2
[0045] The preparation of magnesium hydroxide composite agglomerated particles comprises the following steps:
[0046] Step 1, in 20kg magnesium nitrate solution, add nano silicon dioxide powder 5kg and nano titanium dioxide powder 4kg to disperse uniformly, the mass concentration of magnesium nitrate solution is 20%, obtain mixed solution, add ammonia water to mixed solution, adjust pH value to 8 , to prepare coated particles with nano-silica powder and nano-titanium dioxide powder as the core, filter and dry them to obtain a solid product;
[0047] In step 2, 3 kg of mica powder and 9 kg of polyethylene glycol are added to the solid product, and spray granulation is carried out to obtain magnesium hydroxide composite agglomerated particles with a particle size of less than 0.1 mm.
preparation example 3
[0049] The preparation of magnesium hydroxide composite agglomerated particles comprises the following steps:
[0050] Step 1, adding 4.2 kg of nano-silicon dioxide powder and 2.8 kg of nano-titania powder to the 20kg magnesium nitrate solution to disperse uniformly, the mass concentration of the magnesium nitrate solution is 20%, to obtain a mixed solution, add ammonia water to the mixed solution, and adjust the pH value To 9, the coated particles with nano-silicon dioxide powder and nano-titanium dioxide powder as inner cores are prepared, filtered and dried to obtain a solid product;
[0051] In step 2, 2.3 kg of mica powder and 7.9 kg of polyethylene glycol are added to the solid product, and spray granulation is carried out to obtain magnesium hydroxide composite agglomerated particles with a particle size of less than 0.1 mm.
PUM
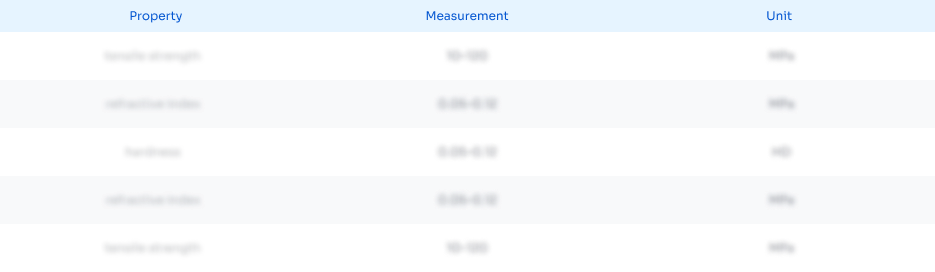
Abstract
Description
Claims
Application Information

- R&D
- Intellectual Property
- Life Sciences
- Materials
- Tech Scout
- Unparalleled Data Quality
- Higher Quality Content
- 60% Fewer Hallucinations
Browse by: Latest US Patents, China's latest patents, Technical Efficacy Thesaurus, Application Domain, Technology Topic, Popular Technical Reports.
© 2025 PatSnap. All rights reserved.Legal|Privacy policy|Modern Slavery Act Transparency Statement|Sitemap|About US| Contact US: help@patsnap.com