Acid zinc-nickel alloy electroplating additive and electroplating solution
An electroplating additive and zinc-nickel alloy technology, applied in the field of electroplating, can solve the problems of increased energy consumption and production cost, difficulty in obtaining a zinc-nickel coating, poor plating ability of the plating solution, etc., so as to improve the leveling ability and gloss, improve The effect of pinhole pitting appearance, optimal flatness and gloss
- Summary
- Abstract
- Description
- Claims
- Application Information
AI Technical Summary
Problems solved by technology
Method used
Image
Examples
Embodiment 1
[0037] The configuration process of acid zinc-nickel alloy electroplating additives and electroplating solution is as follows:
[0038] (1) Add 500mL of pure water in a container with a volume of 1L and heat it in a water bath. When the temperature of the water rises to about 40°C, add 45g of zinc chloride, 110g of nickel chloride and 110g of potassium chloride in turn to fully stir to obtain a mixed solution. liquid A;
[0039] (2) 20.3g of 4-phenyl-3-butene-2-one, 9g of butynediol and 15.8g of o-benzosulfimide were successively added to the mixed solution A and stirred to be fully dissolved; Then add 7.5g of sodium benzoate, 15g of triethanolamine, 7.5g of sodium salicylate in sequence and mix well; finally, add 56mL of polyethylene polyamine, 49mL of sodium ethanesulfonate, and 35mL of PEG-600 in sequence, fully stir and dissolve to make it evenly mixed, to obtain mixed solution B;
[0040] (3) adding boric acid to adjust the pH value of the mixed solution B in the range ...
Embodiment 2
[0044] The configuration process of acid zinc-nickel alloy electroplating additives and electroplating solution is as follows:
[0045] (1) Add 500mL of pure water in a container with a volume of 1L and heat it in a water bath. When the temperature of the water rises to about 40°C, add 45g of zinc chloride, 100g of nickel chloride and 120g of potassium chloride in turn to fully stir to obtain a mixed solution. liquid A;
[0046] (2) successively add 20g of 4-phenyl-3-buten-2-one, 12.5g of butynediol, 17.5g of phthalimide to the mixed solution A and stir to fully dissolve it; Then add 12g of sodium benzoate, 18g of triethanolamine, 10g of sodium salicylate in sequence and mix well; finally add 53mL of polyethylene polyamine, 45mL of sodium ethanesulfonate, and 42mL of PEG-600 in sequence, fully stir and dissolve to make the mixture uniform, and obtain a mixed solution. liquid B;
[0047](3) adding boric acid to adjust the pH value of the mixed solution B in the range of 5.0-5...
Embodiment 3
[0051] The configuration process of acid zinc-nickel alloy electroplating additives and electroplating solution is as follows:
[0052] (1) Add 500mL of pure water in a container with a volume of 1L and heat it in a water bath. When the temperature of the water rises to about 40°C, add 40g of zinc chloride, 120g of nickel chloride and 100g of potassium chloride in turn to fully stir to obtain a mixed solution. liquid A;
[0053] (2) 22.5 g of 4-phenyl-3-buten-2-one, 11.3 g of butynediol, and 11.3 g of o-benzothiimide were sequentially added to the mixed solution A, and stirred to fully dissolve ; Then add 7.5g sodium benzoate, 11.3g triethanolamine, 6.3g sodium salicylate in turn and mix; finally add 58mL polyvinylpolyamine, 50mL sodium ethanesulfonate, 37mL PEG-600 in turn, fully stir and dissolve to make them mix uniform to obtain mixed solution B;
[0054] (3) adding boric acid to adjust the pH value of the mixed solution B in the range of 5.0-5.5, adding pure water to th...
PUM
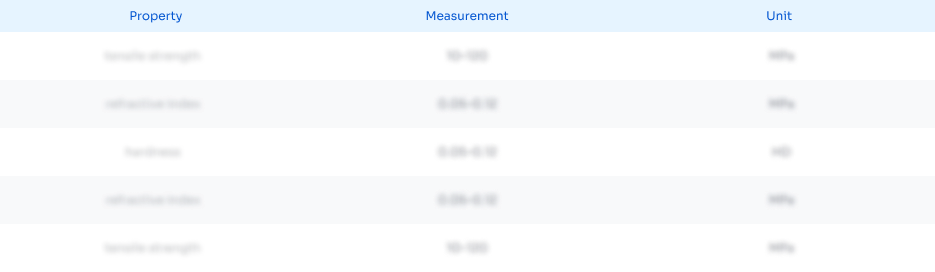
Abstract
Description
Claims
Application Information

- R&D Engineer
- R&D Manager
- IP Professional
- Industry Leading Data Capabilities
- Powerful AI technology
- Patent DNA Extraction
Browse by: Latest US Patents, China's latest patents, Technical Efficacy Thesaurus, Application Domain, Technology Topic, Popular Technical Reports.
© 2024 PatSnap. All rights reserved.Legal|Privacy policy|Modern Slavery Act Transparency Statement|Sitemap|About US| Contact US: help@patsnap.com