Motor pouring sealant and preparation method thereof
A potting glue and mixer technology, applied in the field of potting glue, can solve the problems such as the lack of significant performance improvement in mechanical properties, poor thermal conductivity, and low thermal conductivity and dispersion density of silicone potting glue, so as to improve mechanical properties. Material properties, improving thermal conductivity, and the effect of improving cross-linking density
- Summary
- Abstract
- Description
- Claims
- Application Information
AI Technical Summary
Problems solved by technology
Method used
Image
Examples
Embodiment 1
[0031] A motor potting glue, comprising the following raw materials in parts by weight: 90-100 parts of linear-terminated vinyl silicone oil, 100 parts of thermally conductive filler, 30 parts of alicyclic epoxy resin, 10 parts of crosslinking agent, 2 parts of catalyst, 4 parts of surfactant, 8 parts of gas phase black and white carbon, 100 parts of water.
[0032] Further, the thermally conductive filler is a mixture of glass fiber, graphite powder and titanium dioxide powder, and the mass ratio of glass fiber, graphite powder and titanium dioxide powder in the thermally conductive filler is 1:2:1.
[0033] Further, the catalyst is a platinum catalyst.
[0034] Further, the crosslinking agent is tetra-n-propyl zirconate.
[0035] Further, the surfactant is vinyltriethoxysilane.
[0036] The present invention also provides a preparation method of motor potting glue, comprising the following steps:
[0037] Step 1: Add surfactant into the thermally conductive filler, ultras...
Embodiment 2
[0045] The motor potting glue provided in this example and its preparation method are roughly the same as those in Example 1, the main difference is that it includes the following raw materials in parts by weight: 95 parts of linear terminal vinyl silicone oil, 110 parts of thermally conductive filler, 35 parts of cycloaliphatic epoxy resin, 12 parts of cross-linking agent, 4 parts of catalyst, 6 parts of surfactant, 10 parts of gas-phase method black and white carbon, 110 parts of water;
[0046] In step 1, ultrasonically mix for 40 minutes, then add water to continue ultrasonic mixing for 35 minutes, and ultrasonically mix with a power of 21w;
[0047] In step 2, the cycloaliphatic epoxy resin was melted at a temperature of 100°C, the speed of the mixer was 520r / min, and the stirring time was 117min;
[0048] In step 3, under the condition of temperature of 87°C, mix material A and material B in a mixer, and degas it by ultrasonic for 7 minutes, the rotation speed of the mix...
Embodiment 3
[0050] A motor potting glue provided in this embodiment and its preparation method are roughly the same as in Embodiment 1, the main difference is that it includes the following raw materials in parts by weight: 100 parts of linear-terminal vinyl silicone oil, 120 parts of thermally conductive filler, 40 parts of cycloaliphatic epoxy resin, 14 parts of crosslinking agent, 6 parts of catalyst, 8 parts of surfactant, 12 parts of gas-phase method black and white carbon, 120 parts of water;
[0051] In step 1, ultrasonically mix for 30-50 minutes, then add water and continue to ultrasonically mix for 40 minutes, and ultrasonically mix with a power of 23w;
[0052] In step 2, the cycloaliphatic epoxy resin is melted at a temperature of 90-110°C, the speed of the mixer is 600r / min, and the stirring time is 20min;
[0053] In step 3, under the condition of temperature of 95°C, mix material A and material B in a mixer, and degas it by ultrasonic for 10 minutes, the rotation speed of t...
PUM
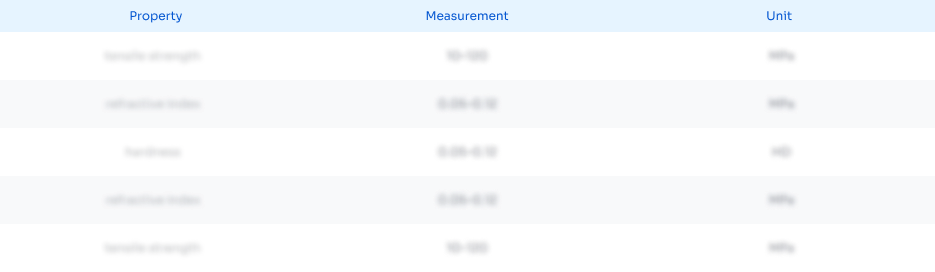
Abstract
Description
Claims
Application Information

- R&D Engineer
- R&D Manager
- IP Professional
- Industry Leading Data Capabilities
- Powerful AI technology
- Patent DNA Extraction
Browse by: Latest US Patents, China's latest patents, Technical Efficacy Thesaurus, Application Domain, Technology Topic, Popular Technical Reports.
© 2024 PatSnap. All rights reserved.Legal|Privacy policy|Modern Slavery Act Transparency Statement|Sitemap|About US| Contact US: help@patsnap.com