Method for reducing smelting cost of converter
A converter smelting and cost technology, applied in the direction of manufacturing converters, etc., can solve the problems of gas waste, affecting the quality of molten steel, temperature waste, etc., and achieve the effect of obvious cooling effect, shortening cooling time, and strong operability.
- Summary
- Abstract
- Description
- Claims
- Application Information
AI Technical Summary
Problems solved by technology
Method used
Examples
Embodiment Construction
[0013] The following are specific examples of the present invention, further describing the technical solutions of the present invention, but the protection scope of the present invention is not limited to these examples. All changes or equivalent substitutions that do not depart from the concept of the present invention are included in the protection scope of the present invention.
[0014] A method for reducing converter smelting costs, comprising the steps of:
[0015] 1) Add a steel bar cutting head silo on the furnace front platform, install a vibrating screen at the lower end of the steel bar cutting head silo, and use a scrap steel bucket to add the steel bar cutting head into the steel bar cutting head silo;
[0016] 2) Use a forklift to pick up the cold hopper, place it under the vibrating screen of the steel bar cutting head bin, start the vibrating screen to vibrate the steel bar cutting head into the cold hopper;
[0017] 3) Use a forklift to transport the cut hea...
PUM
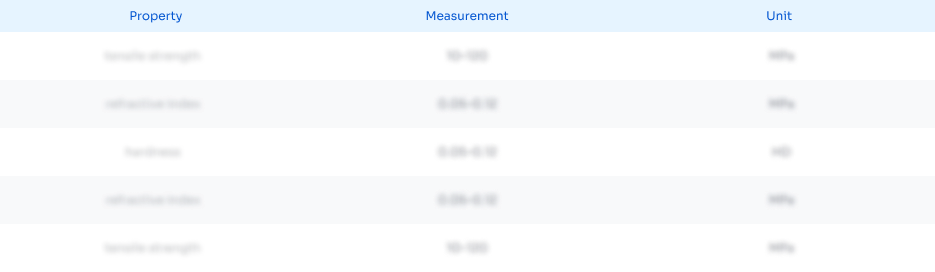
Abstract
Description
Claims
Application Information

- R&D
- Intellectual Property
- Life Sciences
- Materials
- Tech Scout
- Unparalleled Data Quality
- Higher Quality Content
- 60% Fewer Hallucinations
Browse by: Latest US Patents, China's latest patents, Technical Efficacy Thesaurus, Application Domain, Technology Topic, Popular Technical Reports.
© 2025 PatSnap. All rights reserved.Legal|Privacy policy|Modern Slavery Act Transparency Statement|Sitemap|About US| Contact US: help@patsnap.com