Method for extracting vanadium from low-grade vanadium-containing raw material and recycling wastewater
A waste water circulation and low-grade technology, applied in the field of vanadium extraction and metallurgy, can solve the problems of unqualified vanadium product quality, sodium salt influence, etc., and achieve the effect of good application prospects
- Summary
- Abstract
- Description
- Claims
- Application Information
AI Technical Summary
Problems solved by technology
Method used
Image
Examples
Embodiment 1
[0068] (1) Add 1000g of the stone coal roasting clinker in Table 1 and 8g of calcium sulfite to 2000mL of water for beating, then add sulfuric acid, and leaching under stirring conditions, the leaching temperature is 25°C, and the leaching time is 100min , the pH value of leaching is 1.5, uses lime to adjust the pH value of system to 2.3 after leaching finishes, then solid-liquid separation obtains 1029g residue (V 2 o 5 content is 0.21% by weight) and leaching solution, the rate of vanadium transfer leaching is 81.54%;
[0069] (2) Utilize magnesium carbonate to adjust the pH value of the leachate to 6.5 to carry out vanadium precipitation, then filter to obtain vanadium precipitate and primary waste water (TV is 0.02g / L);
[0070] (3) Add 150mL of water (the liquid-solid ratio of water to vanadium precipitate is 11mL / g), 0.8g of zirconium sulfate and sulfuric acid to the vanadium precipitate, and react at 120°C for 30min while stirring, and the pH of the reaction is Value ...
Embodiment 2
[0075] (1) Add 1000g of vanadium ore roasting clinker and 9g of calcium sulfite in 2000mL of water for beating, then add sulfuric acid, and leaching under stirring conditions, the leaching temperature is 25°C, and the leaching time is 120min , the pH value of leaching is 0.8, uses lime to adjust the pH value of system to 2.5 after leaching finishes, then solid-liquid separation obtains 1030g residue (V 2 o 5 content is 0.22% by weight) and leaching solution, the rate of vanadium transfer leaching is 81.21%;
[0076] (2) Utilize magnesium carbonate to adjust the pH value of the leachate to 6.7 to carry out vanadium precipitation, then filter to obtain vanadium precipitate and primary waste water (TV is 0.02g / L);
[0077] (3) Add 180mL of water (the liquid-solid ratio of water to vanadium precipitate is 13mL / g), 1g of zirconium sulfate and sulfuric acid to the vanadium precipitate, and react at 110°C for 60min while stirring, the pH value of the reaction is Be 2.6, solid-liqui...
Embodiment 3
[0082] (1) Add 1000g of the vanadium extraction tailings in Table 1 and 19g of calcium sulfite to 1500mL of water for beating, then add sulfuric acid, and leaching under stirring conditions, the leaching temperature is 25°C, and the leaching time is 20min, The pH value of leaching is 0.9, uses lime to adjust the pH value of system to 2.7 after leaching finishes, then solid-liquid separation obtains 1043g residue (V 2 o 5 content is 0.81% by weight) and leaching solution, the rate of vanadium transfer leaching is 65.33%;
[0083] (2) Utilize magnesium carbonate to adjust the pH value of the leachate to 6.7 to carry out vanadium precipitation, then filter to obtain vanadium precipitate and primary waste water (TV is 0.02g / L);
[0084] (3) Add 250mL water (the liquid-solid ratio of water and vanadium precipitate is 11.5mL / g), 1.2g zirconium sulfate and sulfuric acid in the vanadium precipitate, under the condition of stirring, react at 120 ℃ for 60min, the reaction The pH value...
PUM
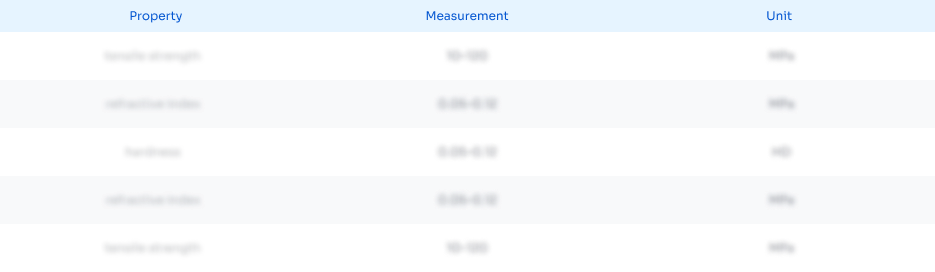
Abstract
Description
Claims
Application Information

- Generate Ideas
- Intellectual Property
- Life Sciences
- Materials
- Tech Scout
- Unparalleled Data Quality
- Higher Quality Content
- 60% Fewer Hallucinations
Browse by: Latest US Patents, China's latest patents, Technical Efficacy Thesaurus, Application Domain, Technology Topic, Popular Technical Reports.
© 2025 PatSnap. All rights reserved.Legal|Privacy policy|Modern Slavery Act Transparency Statement|Sitemap|About US| Contact US: help@patsnap.com