Preparation method of isopropanol
A technology of isopropanol and propylene, which is applied in the field of preparation of isopropanol, can solve problems such as the complex follow-up process of propylene monomer, achieve the effects of reducing equipment maintenance costs, promoting positive reactions, and reducing investment costs
- Summary
- Abstract
- Description
- Claims
- Application Information
AI Technical Summary
Problems solved by technology
Method used
Image
Examples
preparation example Construction
[0028] According to an exemplary embodiment of the present invention, there is provided a method for preparing isopropanol, the method comprising: supplying a supply stream comprising propylene monomer and water to a reaction unit, so that the propylene monomer and water react with each other, thereby A reaction product comprising isopropanol, propylene monomer and water is produced; the first discharge stream comprising the gaseous reaction product discharged from the reaction unit and the second discharge stream comprising the liquid phase reaction product discharged from the reaction unit are Each is supplied to a stripper 200; and a top discharge stream comprising propylene monomer and a bottom discharge stream comprising water and isopropanol are separated from the stripper 200, wherein the first discharge stream passes through a first heat exchanger 310 is condensed and supplied to the stripper 200 in the liquid phase.
[0029] According to an exemplary embodiment of the...
example 1
[0054] like figure 1 As shown in the process flow diagram shown in , isopropanol (IPA) is prepared and the unreacted product and isopropanol are separated.
[0055] Specifically, feed the supply flow to 40kg / cm at a flow rate of 134ton / hr 2 Reactor 100 working at a pressure of g, and will supply the water in the stream (H 2 The ratio of O) to propylene monomer (PP) is controlled to be 0.4. In this case, the supply stream passes through the second heat exchanger 320 and is then supplied to the reactor 100 .
[0056] The discharge stream of the reactor 100 is separated into a first discharge stream and a second discharge stream while passing through the second heat exchanger 320 and then discharged, and the first discharge stream is condensed in the first heat exchanger 310 and then supplied to the steam The 1st rung of Titta 200. In addition, the second effluent stream is fed to the fifth stage of the stripper 200 .
[0057] The stripper 200 operates at atmospheric pressu...
example 2
[0060] like figure 2 As shown in the process flow diagram shown in , isopropanol is prepared and the unreacted product and isopropanol are separated.
[0061]Specifically, feed the supply flow to 40kg / cm at a flow rate of 134ton / hr 2 The reactor 100 was operated at a pressure of g, and the ratio of water to propylene monomer in the feed stream was controlled to be 0.4. In this case, the supply stream passes through the second heat exchanger 320 and is then supplied to the reactor 100 .
[0062] The effluent stream of the reactor 100 is separated into a first effluent stream and a second effluent stream while passing through the second heat exchanger 320 and then discharged, and the first effluent stream is condensed in the first heat exchanger 310 and then fed to the stripper 1st rung of tower 200. In addition, the second effluent stream is fed to the fifth stage of the stripper 200 . In this case, a separate condenser (not shown) is arranged to further condense the uncon...
PUM
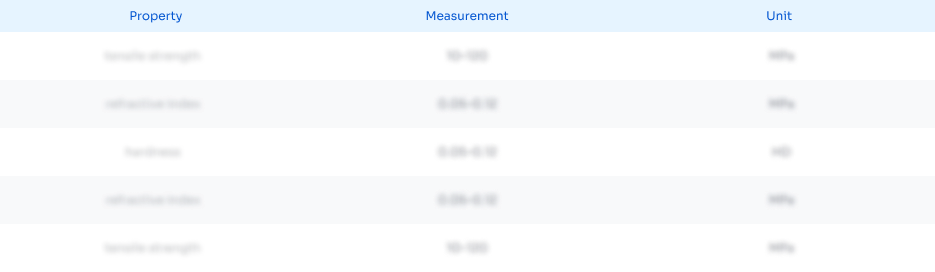
Abstract
Description
Claims
Application Information

- Generate Ideas
- Intellectual Property
- Life Sciences
- Materials
- Tech Scout
- Unparalleled Data Quality
- Higher Quality Content
- 60% Fewer Hallucinations
Browse by: Latest US Patents, China's latest patents, Technical Efficacy Thesaurus, Application Domain, Technology Topic, Popular Technical Reports.
© 2025 PatSnap. All rights reserved.Legal|Privacy policy|Modern Slavery Act Transparency Statement|Sitemap|About US| Contact US: help@patsnap.com