Printing and reinforcement method for 3D printing concrete member
A 3D printing and concrete technology, which is applied in the direction of building components, structural elements, building reinforcements, etc., can solve problems such as inability to play a strengthening role, and achieve the effect of ensuring integrity and relative position, sufficient reinforcement, and preventing damage
- Summary
- Abstract
- Description
- Claims
- Application Information
AI Technical Summary
Problems solved by technology
Method used
Image
Examples
Embodiment 1
[0055] Prepare concrete according to the mix ratio in Table 1:
[0056] Table 1 Mix #1
[0057]
[0058] Note: The amount of cellulose ether, sodium gluconate, and polycarboxylate superplasticizer is calculated based on the amount of cement.
[0059] Concrete is prepared and mixed according to the above mixing ratio. When mixing the concrete, there should be no segregation or bleeding. After mixing fully, the measured slump is 120mm; when printing, it is observed that the concrete is continuous and uniform, without clogging, and without obvious cracks. Cracked, the shape remains stable and does not collapse;
[0060] The component is a beam component, the size is 240×600×2000, the size of the extruded single-layer concrete is 30mm×100mm, and 8 layers are printed;
[0061] Reinforcement according to figure 1 The grid configuration shown, the relevant parameters α = 45°, θ = 45°, four HRB400 with a diameter of 16mm are equipped in the tension area, and the compression area...
Embodiment 2
[0067] Prepare concrete according to mix ratio #2 in Table 3:
[0068] Table 3 Mix #2
[0069]
[0070] Note: The amount of cellulose ether, sodium gluconate, and polycarboxylate superplasticizer is calculated based on the amount of cement.
[0071] Concrete is prepared and mixed according to the above mixing ratio. When mixing the concrete, there should be no segregation or bleeding. After mixing fully, the measured slump is 120mm; when printing, it is observed that the concrete is continuous and uniform, without clogging, and without obvious cracks. Cracked, the shape remains stable and does not collapse;
[0072] The component is a beam component, the size is 240×600×2000, the size of the extruded single-layer concrete is 30mm×100mm, and 8 layers are printed;
[0073] Reinforcement according to figure 1 The grid configuration shown, the relevant parameters α = 45°, θ = 45°, four HRB400 with a diameter of 16mm are equipped in the tension area, and the compression area ...
Embodiment 3
[0079] Embodiment 3 comparative example
[0080] Prepare concrete according to mix ratio #3 in Table 5:
[0081] Table 5 Mix #2
[0082]
[0083] Note: The amount of cellulose ether, sodium gluconate, and polycarboxylate superplasticizer is calculated based on the amount of cement.
[0084] Concrete was prepared and stirred according to the above mixing ratio. When the concrete was mixed, segregation and bleeding occurred. After mixing fully, the slump was measured to be 180mm; when printing, it was observed that the concrete was continuous and not clogged, but uneven. Print the upper layer During concrete, the form of the lower concrete is easily deformed and collapsed, making it impossible to print. Therefore, the printing performance requirements pointed out in the present invention are required to prepare concrete.
PUM
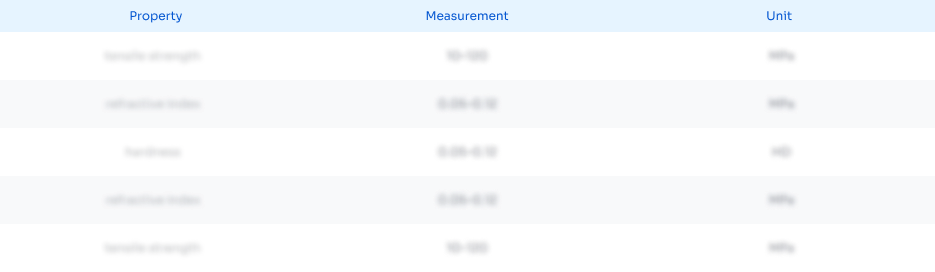
Abstract
Description
Claims
Application Information

- R&D Engineer
- R&D Manager
- IP Professional
- Industry Leading Data Capabilities
- Powerful AI technology
- Patent DNA Extraction
Browse by: Latest US Patents, China's latest patents, Technical Efficacy Thesaurus, Application Domain, Technology Topic, Popular Technical Reports.
© 2024 PatSnap. All rights reserved.Legal|Privacy policy|Modern Slavery Act Transparency Statement|Sitemap|About US| Contact US: help@patsnap.com