Regeneration method of hydrogenation catalyst
A hydrogenation catalyst and catalyst technology, which are applied in catalyst regeneration/reactivation, chemical instruments and methods, physical/chemical process catalysts, etc., can solve the problems that the physical and chemical properties and structures of hydrogenation catalysts cannot meet the requirements of industrial production, etc. To achieve the effect of improving catalyst performance, avoiding the formation of hot spots, and having a wide range of applications
- Summary
- Abstract
- Description
- Claims
- Application Information
AI Technical Summary
Problems solved by technology
Method used
Examples
Embodiment 1
[0042] (1) After sampling the deactivated sulfided residue hydrogenation catalyst from the reaction device, seal it with ethanol liquid. Using a fat extractor, the above-mentioned catalyst is immersed in toluene solution, heated to a boiling state of toluene and refluxed to condense for 24 hours, after the extraction is completed, vacuum-dried to obtain deactivated catalyst A1 (in the form of deactivated hydrogenation catalyst A1 Based on the weight of the source fresh catalyst, the content of the active metal molybdenum in terms of oxides is 16%; based on the weight of the source fresh catalyst of the deactivated hydrogenation catalyst, the contained deposition metal iron and vanadium, in terms of metal elemental total content is 1.33%).
[0043] (2) After sampling and taking out the deactivated sulfurized bulk hydrofining catalyst from the reaction device, seal it with ethanol liquid. Using a fat extractor, immerse the above catalyst in toluene solution, heat to the boiling...
Embodiment 2
[0050] (1) After sampling the deactivated sulfided residue hydrogenation catalyst from the reaction device, seal it with ethanol liquid. Using a fat extractor, the above-mentioned catalyst is immersed in toluene solution, heated to a boiling state of toluene and refluxed to condense for 24 hours, after the extraction is completed, vacuum-dried to obtain deactivated catalyst A1 (in the form of deactivated hydrogenation catalyst A1 Based on the weight of the source fresh catalyst, the content of the active metal molybdenum in terms of oxides is 16%; based on the weight of the source fresh catalyst of the deactivated hydrogenation catalyst, the contained deposition metal iron and vanadium, in terms of metal elemental total content is 1.33%).
[0051] (2) After sampling and taking out the deactivated sulfurized bulk hydrofining catalyst from the reaction device, seal it with ethanol liquid. Using a fat extractor, immerse the above catalyst in toluene solution, heat to the boiling...
Embodiment 3
[0058] (1) After sampling the deactivated sulfided residue hydrogenation catalyst from the reaction device, seal it with ethanol liquid. Using a fat extractor, the above-mentioned catalyst is immersed in toluene solution, heated to a boiling state of toluene and refluxed to condense for 24 hours, after the extraction is completed, vacuum-dried to obtain deactivated catalyst A1 (in the form of deactivated hydrogenation catalyst A1 Based on the weight of the source fresh catalyst, the content of the active metal molybdenum in terms of oxides is 16%; based on the weight of the source fresh catalyst of the deactivated hydrogenation catalyst, the contained deposition metal iron and vanadium, in terms of metal elemental total content is 1.33%).
[0059] (2) After sampling and taking out the deactivated sulfurized bulk hydrofining catalyst from the reaction device, seal it with ethanol liquid. Using a fat extractor, immerse the above catalyst in toluene solution, heat to the boiling...
PUM
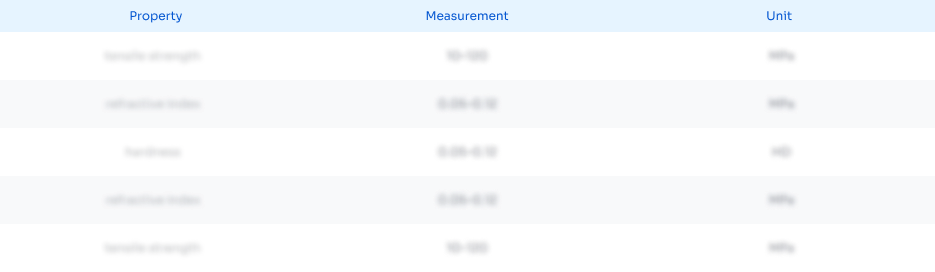
Abstract
Description
Claims
Application Information

- Generate Ideas
- Intellectual Property
- Life Sciences
- Materials
- Tech Scout
- Unparalleled Data Quality
- Higher Quality Content
- 60% Fewer Hallucinations
Browse by: Latest US Patents, China's latest patents, Technical Efficacy Thesaurus, Application Domain, Technology Topic, Popular Technical Reports.
© 2025 PatSnap. All rights reserved.Legal|Privacy policy|Modern Slavery Act Transparency Statement|Sitemap|About US| Contact US: help@patsnap.com