Austenitic stainless steel D-type thin-wall pipe forming process
A technology for austenitic stainless steel and thin-walled pipes, which is applied in manufacturing tools, metal processing equipment, metal wire drawing, etc., and can solve problems such as difficulty in improving production efficiency, uneven tensile stress, and large tensile anisotropy. Achieve the effects of improving production efficiency, reducing the number of stretching times, and high surface quality
- Summary
- Abstract
- Description
- Claims
- Application Information
AI Technical Summary
Problems solved by technology
Method used
Image
Examples
Embodiment 1
[0024] The present embodiment prepares a kind of lubricant, and specific implementation process is as follows:
[0025] Step 1: Weigh commercially available graphite and dry it to constant weight, fully grind it in a dry ball mill, sieve the grinding material through a 300-mesh sieve, and take the sieved powder to obtain graphite powder;
[0026] Step 2: Measure 1L of finished drawing oil, 50g of graphite powder prepared in Step 1 and 150mL of sodium petroleum sulfonate into a high-speed shearing machine, stir fully at a speed of 1500r / min for 15min to obtain a viscous mixed oil, and then reduce Rotate at 180r / min, add liquid wax to the mixed oil until the adjusted viscosity is 13±2mm at 60°C 2 / s, made into a lubricant.
[0027] In the example:
[0028] Drawing oil selection drawing oil C63-1;
Embodiment 2
[0031] In this example, a D-shaped thin-walled pipe is stretched and formed, and 316L austenitic stainless steel is selected. Please refer to figure 1 As shown, the specific implementation process is as follows:
[0032] Process S1, intermediate pipe stretching:
[0033] 1) Select a coil of 316L austenitic stainless steel circular welded coil, and its nominal size is φ9.1*0.3;
[0034] 2) Use the unwinding machine to unwind the coiled pipe. The pipe passes through the online heating equipment, and the pipe is subjected to solution heat treatment. The heat treatment temperature is set at 1070°C, and the heat treatment speed is 4m / min. Apply the sponge soaked with the lubricant prepared in Example 1, apply the lubricant evenly on the surface of the pipe, and then stretch the pipe through a drawing die to reduce the diameter and thickness of the pipe. The size of the pipe after stretching is φ8.3*0.265, get a stretched tube;
[0035] 3) In the same way as in process 2), perfor...
PUM
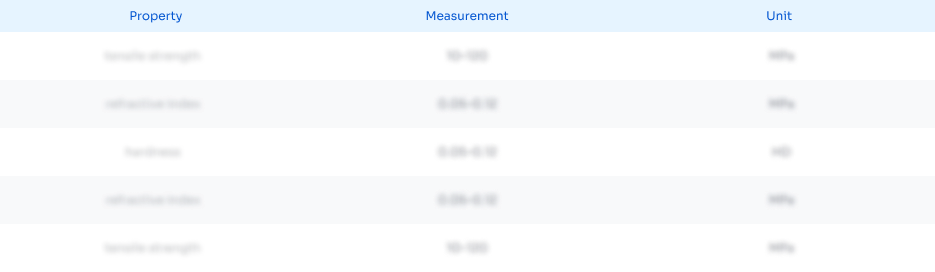
Abstract
Description
Claims
Application Information

- R&D Engineer
- R&D Manager
- IP Professional
- Industry Leading Data Capabilities
- Powerful AI technology
- Patent DNA Extraction
Browse by: Latest US Patents, China's latest patents, Technical Efficacy Thesaurus, Application Domain, Technology Topic, Popular Technical Reports.
© 2024 PatSnap. All rights reserved.Legal|Privacy policy|Modern Slavery Act Transparency Statement|Sitemap|About US| Contact US: help@patsnap.com