Digital transfer printing method using plant dye ink
A vegetable dye and transfer printing technology, which is applied in transfer printing, dyeing, copying/marking methods, etc., can solve the problems of large environmental pollution, unsuitable for natural fiber fabrics, and low controllability of printing effects
- Summary
- Abstract
- Description
- Claims
- Application Information
AI Technical Summary
Problems solved by technology
Method used
Image
Examples
Embodiment 1
[0077] (1) Coating the paste on the surface of blank paper, then drying and calendering, to obtain transfer paper;
[0078] (2) 20g of humectant (N-methylpyrrolidone) and part of ultrapure water are mechanically stirred and mixed to obtain humectant solution, and then 7g of plant dye (carmine) is mixed with part of ultrapure water to obtain plant dye color slurry, add vegetable dye color paste, 0.3g surface tension regulator (fatty acid sorbitan ester), 1g viscosity regulator (polyvinylpyrrolidone and carboxymethyl chitosan), 0.4g pH buffering agent to the humectant solution successively agent (methylethanolamine), 1g antiseptic and bactericide (sodium benzoate and potassium sorbate) and the remaining ultrapure water, then stirred (the time of stirring was 2h, and the speed of stirring was 600r / min) and ultrasonic treatment (ultrasonic treatment The time is 30min, the power of ultrasonic treatment is 600w), and then successively filtered through 0.45μm and 0.22μm water-based f...
Embodiment 2
[0083] (1) Coating the paste on the surface of blank paper, then drying and calendering, to obtain transfer paper;
[0084] (2) 20g humectant (diethylene glycol) and part of ultrapure water are mechanically stirred and mixed to obtain humectant solution, then 10g vegetable dye (monascus yellow) is mixed with part of ultrapure water to obtain vegetable dye paste, Add vegetable dye color paste, 0.5g surface tension regulator (coconut oil fatty acid diethanolamide and N-alkyl betaine), 0.2g viscosity regulator (PEG400), 0.5gpH buffering agent (isopropyl Alcohol amine), 0.5g antiseptic bactericide (phenylpropaisothiazolinone) and remaining ultrapure water, then stir (the time of stirring is 2h, the speed of stirring is 800r / min) and ultrasonic treatment (the time of ultrasonic treatment 30min, the power of ultrasonic treatment is 500w), and then sequentially filtered through 0.45μm and 0.22μm water-based filter membranes to obtain vegetable dye ink, wherein the total weight of ult...
Embodiment 3
[0089] (1) Coating the paste on the surface of blank paper, then drying and calendering, to obtain transfer paper;
[0090] (2) 15g humectant (triethylene glycol) and part of ultrapure water are mechanically stirred and mixed to obtain humectant solution, then 15g vegetable dye (hematoxylin) is mixed with part of ultrapure water to obtain vegetable dye paste, Add vegetable dye color paste, 0.2g surface tension modifier (alkylphenol polyoxyethylene ether), 0.7g viscosity modifier (PEG1000), 0.2g pH buffering agent (triethanolamine), 0.1g antiseptic Bactericide (potassium sorbate) and remaining ultrapure water are then stirred (the time of stirring is 2h, and the speed of stirring is 600r / min) and ultrasonic treatment (the time of ultrasonic treatment is 30min, and the power of ultrasonic treatment is 600w) , followed by filtration through 0.45 μm and 0.22 μm water-based filter membranes to obtain vegetable dye ink, wherein the total weight of ultrapure water is 68.8g;
[0091]...
PUM
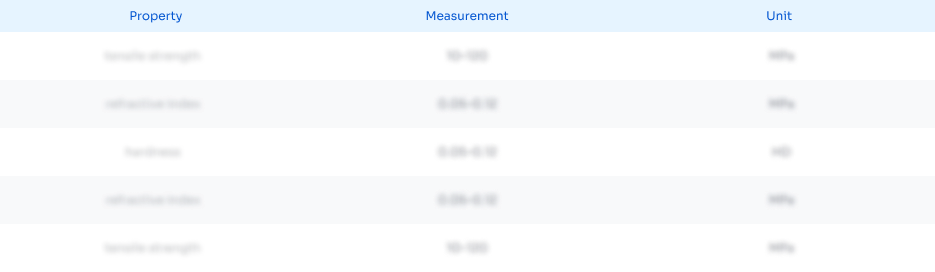
Abstract
Description
Claims
Application Information

- R&D Engineer
- R&D Manager
- IP Professional
- Industry Leading Data Capabilities
- Powerful AI technology
- Patent DNA Extraction
Browse by: Latest US Patents, China's latest patents, Technical Efficacy Thesaurus, Application Domain, Technology Topic, Popular Technical Reports.
© 2024 PatSnap. All rights reserved.Legal|Privacy policy|Modern Slavery Act Transparency Statement|Sitemap|About US| Contact US: help@patsnap.com