Surface carbonitriding treatment method for planet shaft for tractor axle
A carbonitriding, tractor technology, applied in heat treatment furnaces, heat treatment equipment, coatings, etc., can solve the problem of not being able to improve the strength, toughness and fatigue strength of products at the same time, and achieve excellent fatigue resistance and toughness. Effect
- Summary
- Abstract
- Description
- Claims
- Application Information
AI Technical Summary
Problems solved by technology
Method used
Image
Examples
Embodiment 1
[0040] Example 1: A carbonitriding treatment method for the surface of planetary shafts for tractor axles
[0041] Include the following steps:
[0042] 1. Permeation-assisted pretreatment
[0043] (1) Surface treatment
[0044] Anneal the casted planetary shaft at 860°C for 1.2 hours at a high temperature in vacuum, cool to room temperature, and perform surface mechanical grinding after degreasing, derusting, and drying;
[0045] The material of the planet shaft is 40Cr alloy steel;
[0046] The surface is mechanically ground, the vibration frequency of the high-frequency generator is 50 Hz under vacuum conditions, the diameter of the stainless steel projectile is 3 mm, and the processing time is 30 minutes;
[0047] (2) Preparation of permeation-promoting coating solution
[0048] The mass fraction is 14% (NH 4 ) 2 MoO 4 Add citric acid to the aqueous solution to adjust pH=3.4 to obtain acidified (NH 4 ) 2 MoO 4 Aqueous solution; 6 kg Ce 2 (SO 4 ) 3 Dissolve in 20...
Embodiment 2
[0057] Example 2: A carbonitriding treatment method for the surface of planet shafts for tractor axles
[0058] Include the following steps:
[0059] 1. Permeation-assisted pretreatment
[0060] (1) Surface treatment
[0061] Anneal the casted planetary shaft at 840°C for 1 hour in vacuum and high temperature. After cooling to room temperature, perform surface mechanical grinding after degreasing, derusting, and drying;
[0062] The material of the planet shaft is 40Cr alloy steel;
[0063] The surface is mechanically ground, the vibration frequency of the high-frequency generator is 50 Hz under vacuum conditions, the diameter of the stainless steel projectile is 3 mm, and the processing time is 20 minutes;
[0064] (2) Preparation of permeation-promoting coating solution
[0065] The mass fraction is 11% (NH 4 ) 2 MoO 4 Add citric acid to the aqueous solution to adjust pH=3 to obtain acidified (NH 4 ) 2 MoO 4 Aqueous solution; 6 kg Ce 2 (SO 4 ) 3 Dissolve in 24 k...
Embodiment 3
[0074] Example 3: A carbonitriding treatment method for the surface of planet shafts for tractor axles
[0075] Include the following steps:
[0076] 1. Permeation-assisted pretreatment
[0077] (1) Surface treatment
[0078] Anneal the casted planetary shaft at 890°C for 1.5 hours in vacuum and high temperature, cool to room temperature, and perform surface mechanical grinding after degreasing, derusting, and drying;
[0079] The material of the planet shaft is 40Cr alloy steel;
[0080] The surface is mechanically ground, the vibration frequency of the high-frequency generator is 50 Hz under vacuum conditions, the diameter of the stainless steel projectile is 3 mm, and the processing time is 40 minutes;
[0081] (2) Preparation of permeation-promoting coating solution
[0082] The mass fraction is 16% (NH 4 ) 2 MoO 4 Add citric acid to the aqueous solution to adjust pH=4 to obtain acidified (NH 4 ) 2 MoO 4 Aqueous solution; 6.6 kg Ce 2 (SO 4 ) 3 Dissolve in 20 k...
PUM
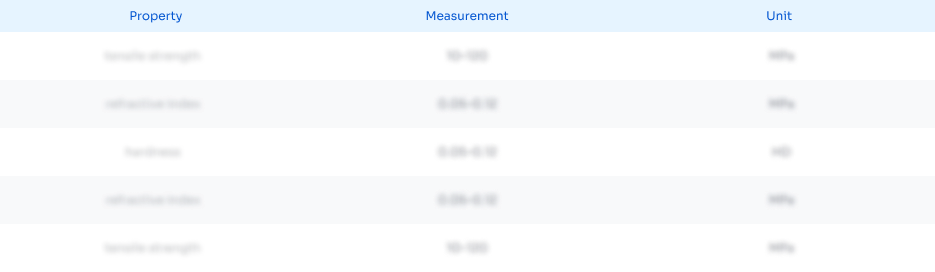
Abstract
Description
Claims
Application Information

- R&D
- Intellectual Property
- Life Sciences
- Materials
- Tech Scout
- Unparalleled Data Quality
- Higher Quality Content
- 60% Fewer Hallucinations
Browse by: Latest US Patents, China's latest patents, Technical Efficacy Thesaurus, Application Domain, Technology Topic, Popular Technical Reports.
© 2025 PatSnap. All rights reserved.Legal|Privacy policy|Modern Slavery Act Transparency Statement|Sitemap|About US| Contact US: help@patsnap.com