Texturing additive with liquid crystal structure, preparation method and application thereof
A liquid crystal structure and additive technology, which is applied in the field of texturing additives with liquid crystal structure and its preparation, can solve the problems of increasing or failing to further increase the pyramid density, unfavorable photoelectric conversion rate of solar cells, etc., and achieves the effect of good texturing performance.
- Summary
- Abstract
- Description
- Claims
- Application Information
AI Technical Summary
Problems solved by technology
Method used
Image
Examples
Embodiment 1
[0023] A texturing additive with a liquid crystal structure, consisting of the following components in weight percent: 0.4% sucrose ester, 0.3% liquid crystal emulsifier, 1.0% polyethylene glycol, 0.3% sodium lignosulfonate, tetrasodium edetate 1.0%, triethanolamine 0.5%, deionized water 96.5%.
[0024] In this embodiment, the HLB of sucrose ester is 11, the liquid crystal emulsifier is C16-18 alkyl glucoside, and the polyethylene glycol is polyethylene glycol 400.
[0025] The preparation method of the texturizing additive with liquid crystal structure comprises the following steps:
[0026] S1. Put sucrose ester and liquid crystal emulsifier into the container by weight, mix with deionized water, heat to 60°C, and keep stirring to obtain A solution;
[0027] S2. Add polyethylene glycol, sodium lignosulfonate, tetrasodium ethylenediaminetetraacetate, and triethanolamine into a container by weight, mix them with deionized water, and heat to 80°C to obtain solution B;
[0028...
Embodiment 2
[0034] A texturing additive with a liquid crystal structure, consisting of the following components in weight percent: 0.4% sucrose ester, 0.3% liquid crystal emulsifier, 1.0% polyethylene glycol, 0.4% sodium lignosulfonate, tetrasodium edetate 1.0%, triethanolamine 0.5%, deionized water 96.4%.
[0035] In this embodiment, the HLB of sucrose ester is 11, the liquid crystal emulsifier is C14-22 alkanol glucoside, and the polyethylene glycol is polyethylene glycol 200.
[0036] The preparation method of the texturizing additive with liquid crystal structure comprises the following steps:
[0037] S1. Put sucrose ester and liquid crystal emulsifier into the container by weight, mix with deionized water, heat to 60°C, and keep stirring to obtain A solution;
[0038] S2. Add polyethylene glycol, sodium lignosulfonate, tetrasodium ethylenediaminetetraacetate, and triethanolamine into a container by weight, mix them with deionized water, and heat to 80°C to obtain solution B;
[00...
Embodiment 3
[0045] A texturing additive with a liquid crystal structure, consisting of the following components in weight percent: 0.4% sucrose ester, 0.3% liquid crystal emulsifier, 1.0% polyethylene glycol, 0.2% sodium lignosulfonate, tetrasodium edetate 1.0%, triethanolamine 0.5%, deionized water 96.6%.
[0046] In this embodiment, the HLB of the sucrose ester is 9, the liquid crystal emulsifier is sorbitan stearate, and the polyethylene glycol is polyethylene glycol 600.
[0047] The preparation method of the texturing additive with liquid crystal structure comprises the following steps:
[0048] S1. Put sucrose ester and liquid crystal emulsifier into the container by weight, mix with deionized water, heat to 60°C, and keep stirring to obtain A solution;
[0049] S2. Add polyethylene glycol, sodium lignosulfonate, tetrasodium ethylenediaminetetraacetate, and triethanolamine into a container by weight, mix them with deionized water, and heat to 80°C to obtain solution B;
[0050] S3...
PUM
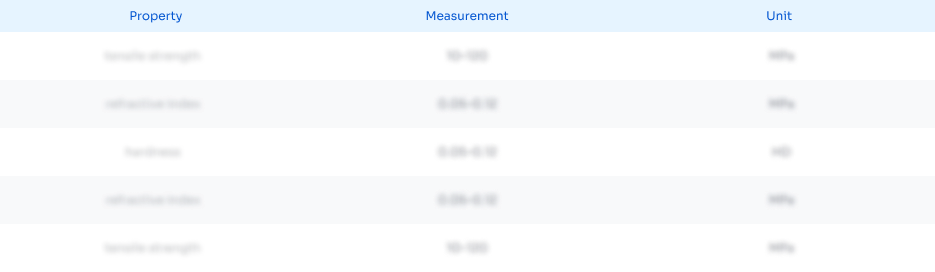
Abstract
Description
Claims
Application Information

- Generate Ideas
- Intellectual Property
- Life Sciences
- Materials
- Tech Scout
- Unparalleled Data Quality
- Higher Quality Content
- 60% Fewer Hallucinations
Browse by: Latest US Patents, China's latest patents, Technical Efficacy Thesaurus, Application Domain, Technology Topic, Popular Technical Reports.
© 2025 PatSnap. All rights reserved.Legal|Privacy policy|Modern Slavery Act Transparency Statement|Sitemap|About US| Contact US: help@patsnap.com