Method for preparing rare earth oxide powder by oxidizing and roasting rare earth mixture
A technology of rare earth mixtures and rare earth oxides, which is applied in the preparation/treatment of rare earth metal compounds, rare earth metal oxides/hydroxides, preparation of chlorides, etc. It is easy to operate, conducive to large-scale promotion and application, and achieves the effect of efficient utilization
- Summary
- Abstract
- Description
- Claims
- Application Information
AI Technical Summary
Problems solved by technology
Method used
Examples
Embodiment 1
[0028] Add 4.8kg yttrium cerium nitrate ((Y 0.9 Ce 0.1 )(NO 3 ) 3 ·6H 2 O, AR), and then heated to 275 ° C for 2 h. Measured precursor band 3.5H 2 O, the molar ratio of crystallization water to nitrate in the precursor is 0.3:1, then the roasted product is ball milled and sieved through a 250-mesh sieve, and the oversize is returned to the ball mill for crushing. The particle size of the precursor after crushing is 56um , the undersize is the precursor. Put this precursor into the roasting furnace, raise the temperature to 850°C, and let air in, the air humidity is 75-85%, and the air flow rate is 120L / min. After reacting for 3 hours, cooling down, the yttrium cerium oxide product with an average particle size of 0.86um can be obtained, the particle size is finer, and the particle size distribution is narrower, the purity is higher, the content of rare earth chloride is 40ppm, and the total amount of rare earth is greater than 99.5%.
Embodiment 2
[0033] Add 6.0kg yttrium cerium chloride ((Y 0.85 Ce 0.15 ) Cl 3 ·7H 2 O, AR), and then heated to 350 °C for 3.5 h. Precursor band 3H was measured 2 O, the molar ratio of crystallization water to chlorine in the precursor is 0.6:1, then the roasted product is crushed by ball milling, and sieved through a 300-mesh screen, and the oversize is returned to the ball mill for crushing. The particle size of the crushed precursor is 23um. The undersize is the precursor. Put this precursor into the roasting furnace, raise the temperature to 600°C, and let air in, the air humidity is 80-90%, and the air flow rate is 280L / min. After reacting for 2 hours, cooling down, the yttrium cerium oxide product with an average particle size of 0.42um can be obtained. The particle size distribution is relatively uniform and the purity is high. The rare earth chloride content is 43ppm and the total rare earth content is greater than 99.5%.
Embodiment 3
[0038] Add 4.8kg samarium gadolinium chloride ((Sm 0.9 Gd 0.1 ) Cl 3 ·6H 2 O, AR), and then heated to 350 °C for 5 h. Precursor band 3H was measured 2 O, the molar ratio of crystallization water to chlorine in the precursor is 0.5:1, then the roasted product is ball milled and sieved through a 250-mesh screen, and the oversize is returned to the ball mill for crushing. The particle size of the crushed precursor is 35um. The undersize is the precursor. Put this precursor into the roasting furnace, raise the temperature to 1060°C, and let air in, the air humidity is 85-95%, and the air flow rate is 350L / min. After reacting for 5 hours, cooling down, the samarium-gadolinium oxide product with an average particle size of 1.22um can be obtained, which has a high purity, a rare earth chloride content of 38ppm, and a total rare earth content of more than 99.5%.
PUM
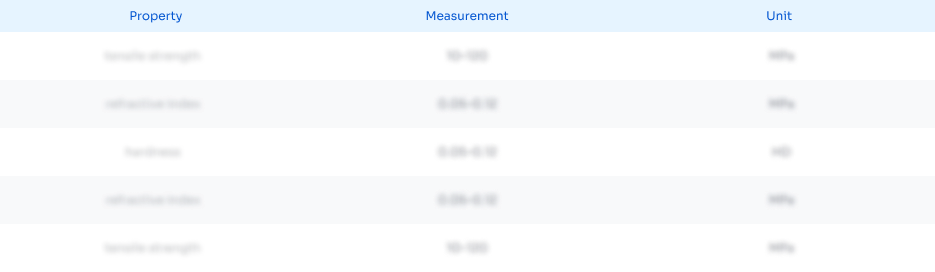
Abstract
Description
Claims
Application Information

- Generate Ideas
- Intellectual Property
- Life Sciences
- Materials
- Tech Scout
- Unparalleled Data Quality
- Higher Quality Content
- 60% Fewer Hallucinations
Browse by: Latest US Patents, China's latest patents, Technical Efficacy Thesaurus, Application Domain, Technology Topic, Popular Technical Reports.
© 2025 PatSnap. All rights reserved.Legal|Privacy policy|Modern Slavery Act Transparency Statement|Sitemap|About US| Contact US: help@patsnap.com