Aluminum alloy and steel optimized welding method based on magnetic control resistance spot welding
A technology of magnetron resistance and welding method, applied in resistance welding equipment, welding equipment, metal processing equipment and other directions, can solve the problems of affecting the mechanical properties of solder joints, difficult to guarantee the quality of joints, unstable quality of solder joints, etc. Stability and consistency, the effect of solving serious electrode wear and improving the surface quality of solder joints
- Summary
- Abstract
- Description
- Claims
- Application Information
AI Technical Summary
Problems solved by technology
Method used
Image
Examples
Embodiment Construction
[0032] Such as figure 1 As shown, it is an optimized welding device for aluminum alloy and steel based on magnetron resistance spot welding in this embodiment, including: an electrode 1 arranged on the steel plate 2 to be connected and a support base 4 arranged under the aluminum plate 3 to be connected , wherein the steel plate 2 to be connected is a dual-phase high-strength steel DP780 with a thickness of 2.0 mm, and the aluminum plate 3 to be connected is an aluminum alloy AA5754 with a thickness of 1.5 mm.
[0033] The electrode 1 includes: an outer electrode rod 101, an inner electrode rod 102, an outer electrode cap 103, and an inner electrode cap 104, wherein: the outer electrode rod 101 and the inner electrode rod 102 are coaxially nested, and the outer electrode cap 103 is arranged on The free end of the outer electrode rod 101 and the inner electrode cap 104 are arranged on the free end of the inner electrode rod 102 .
[0034] The outer electrode cap end 105 is a p...
PUM
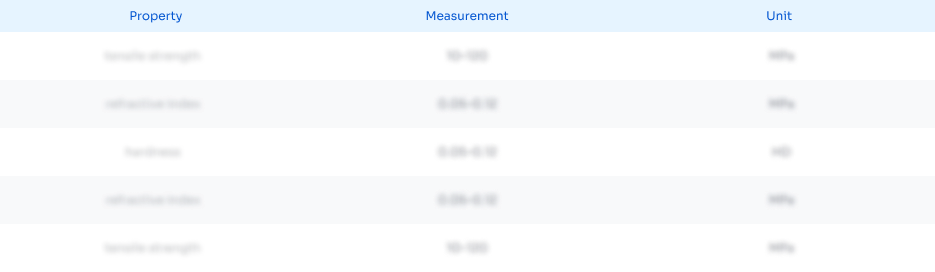
Abstract
Description
Claims
Application Information

- Generate Ideas
- Intellectual Property
- Life Sciences
- Materials
- Tech Scout
- Unparalleled Data Quality
- Higher Quality Content
- 60% Fewer Hallucinations
Browse by: Latest US Patents, China's latest patents, Technical Efficacy Thesaurus, Application Domain, Technology Topic, Popular Technical Reports.
© 2025 PatSnap. All rights reserved.Legal|Privacy policy|Modern Slavery Act Transparency Statement|Sitemap|About US| Contact US: help@patsnap.com