Metal surface treatment electroplating processing method
A technology of metal surface treatment and processing method, applied in metal processing equipment, manufacturing tools, grinding machines, etc., can solve the problems of reducing the quality of electroplating, peeling, peeling, etc., and achieve the effect of improving the quality of electroplating and improving the neatness
- Summary
- Abstract
- Description
- Claims
- Application Information
AI Technical Summary
Problems solved by technology
Method used
Examples
Embodiment 1
[0025] A metal-plating method for processing a metal surface comprising the steps of:
[0026] A. Deancing, cleaning, and drying treatment on the surface of the metal piece: Put the metal member into the oil reducing agent for the removal treatment, and then placed in the cleaning agent for the cleaning treatment, and finally put it in the drying overall to dryness, and The drying temperature is 80-100 ° C, the drying time is 3-8 min, the oil removal is made of organic acid, oxalic acid, trisodium phosphate, boron sand, ethylene glycol butyl ether, dimethylmealone, potassium hydroxide, water, polypropylene The amide, fatty alcohol polyoxyethylene ether sulfate and sodium citrate composition, the components of its weight parts are: 10-15 organic acids; 18-27 oxalate; 6-10 sodium phosphate; boron sand 4-7 Part; ethylene glycol butyl ether; 1-4 dimethylmetone; 2-5 parts of potassium hydroxide; 60-100 parts of water; polyacrylamide 7-15 parts; fatty alcohol polyoxyethylene ether 6-12 ...
Embodiment 2
[0032] A metal-plating method for processing a metal surface comprising the steps of:
[0033] A. Deancing, cleaning, and drying treatment on the surface of the metal piece: Put the metal member into the oil reducing agent for the removal treatment, and then placed in the cleaning agent for the cleaning treatment, and finally put it in the drying overall to dryness, and The drying temperature is 80-100 ° C, the drying time is 3-8 min, and the cleaning agent is made of a defoamer, a cationic surfactant, deionized water, a halogenated hydrocarbon cleaner, diimine, ethanol, trichlorethylene, Zinc nitrate, isopropanol, lignozoate sulfonate and sodium hydroxide composition, the component of its weight fraction is: 8-17 defoamers; 5-10 cationic surfactants; deionized water 80-120 Part; 30-50 parts of halogenated hydrocarbon cleaner; 5-12 dihydrine; 15-23 parts of ethanol; Trichlorethylene 8-12 parts; 6-10 zinc nitrate; isopropyl alcohol 8-15 Die; 4-9 lignin sulfonates; 6-15 sodium hydro...
Embodiment 3
[0039] A metal-plating method for processing a metal surface comprising the steps of:
[0040] A. Deancing, cleaning, and drying treatment on the surface of the metal piece: Put the metal member into the oil reducing agent for the removal treatment, and then placed in the cleaning agent for the cleaning treatment, and finally put it in the drying overall to dryness, and The drying temperature was 80-100 ° C, the drying time was 3-8 min;
[0041] B, cutting and polishing metal parts: cutting and grinding the metal parts by machine tools, making the surface more common;
[0042]C, plating: plasticizing the metal piece into the plating tank and poured into the plating solution in the plating groove, turning on the power supply, so that the metal member is a cathode, the pre-plated cation is deposited in the base metal surface, plating solution Composed of epoxy chloropropane, aluminum sulfate, copper chloride, diisopropanolamide, deionized water, citrate, potassium sulfate, brightene...
PUM
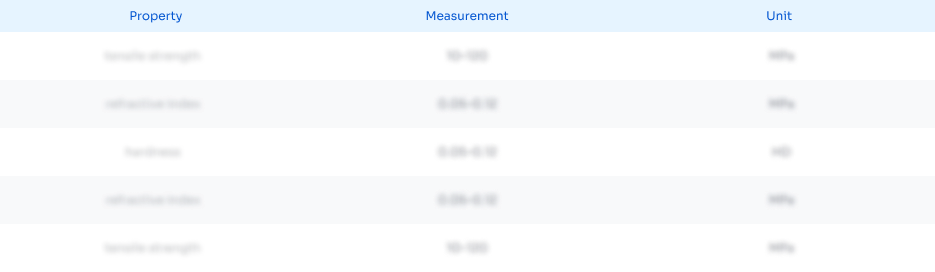
Abstract
Description
Claims
Application Information

- R&D
- Intellectual Property
- Life Sciences
- Materials
- Tech Scout
- Unparalleled Data Quality
- Higher Quality Content
- 60% Fewer Hallucinations
Browse by: Latest US Patents, China's latest patents, Technical Efficacy Thesaurus, Application Domain, Technology Topic, Popular Technical Reports.
© 2025 PatSnap. All rights reserved.Legal|Privacy policy|Modern Slavery Act Transparency Statement|Sitemap|About US| Contact US: help@patsnap.com