Wafer pattern etching method, film resonator assembly and preparation method
A wafer and pattern technology, used in semiconductor/solid-state device manufacturing, electrical components, impedance networks, etc., can solve problems such as difficult sealing, depression, 20 cracks in silicon microcap wafers, etc., to improve yield, improve The degree of sealing and the effect of avoiding stress concentration
- Summary
- Abstract
- Description
- Claims
- Application Information
AI Technical Summary
Problems solved by technology
Method used
Image
Examples
Embodiment Construction
[0045] The present invention will be further described in detail below in conjunction with the accompanying drawings and embodiments. It should be understood that the specific embodiments described here are only used to explain the present invention, but not to limit the present invention. In addition, it should be noted that, for the convenience of description, only some structures related to the present invention are shown in the drawings but not all structures.
[0046] In the embodiment of the present invention, see Figure 14 and Figure 15 The thin film resonator assembly shown, the thin film resonator assembly includes: a device wafer 70, at least one resonant unit is arranged on the device wafer 70; a silicon micro-cap wafer 40, wherein the silicon micro-cap wafer 40 includes a pattern area 40a, the edge-removing area 40b surrounding the graphic area 40a. The pattern area 40a includes an etching pattern 41; the edge-removing area 40b is provided with a bonding layer...
PUM
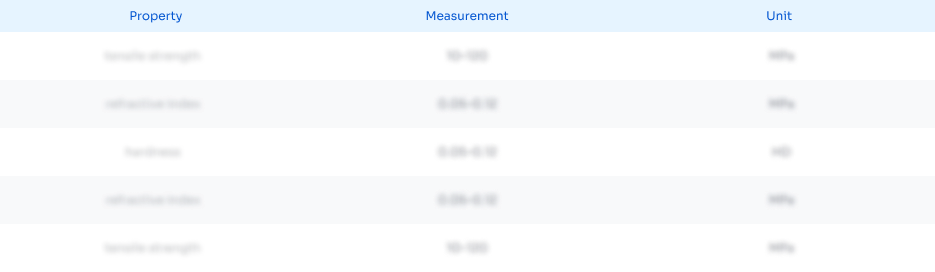
Abstract
Description
Claims
Application Information

- Generate Ideas
- Intellectual Property
- Life Sciences
- Materials
- Tech Scout
- Unparalleled Data Quality
- Higher Quality Content
- 60% Fewer Hallucinations
Browse by: Latest US Patents, China's latest patents, Technical Efficacy Thesaurus, Application Domain, Technology Topic, Popular Technical Reports.
© 2025 PatSnap. All rights reserved.Legal|Privacy policy|Modern Slavery Act Transparency Statement|Sitemap|About US| Contact US: help@patsnap.com