Grinding fluid special for ELID grinding of aluminum-based diamond composite material
A composite material and grinding fluid technology, applied in the petroleum industry, lubricating compositions, etc., can solve the problems of poor surface quality of aluminum-based diamond, clogging of aluminum-based abrasive wheels, and inability to achieve precision machining, etc., to improve grinding processing Surface quality, resistance to deterioration, effects of suppressing excessive electrolysis
- Summary
- Abstract
- Description
- Claims
- Application Information
AI Technical Summary
Problems solved by technology
Method used
Image
Examples
Embodiment 1
[0021] According to the following mass fractions: 2.5% engine oil, 2% soybean oil, 0.3% sodium petroleum sulfonate, 0.1% monoethanolamine benzoate, 0.2% sodium benzoate, 1% polyether ester, 1.8% simethicone , 2.5% molybdenum disulfide, 5.5% polyoxyethylene fatty acid ester, 0.4% chromium oleate, 0.3% triethanolamine, 0.8% benzisothiazolinone, 0.4% methyl benzotriazole, 3 % oxalic acid, 0.3% methyltrimethoxysilane, 0.3% sodium orthosilicate, 0.3% disodium hydrogen phosphate, 0.8% naphthenate, 4.5% tricresyl phosphate, 5% sulfurized fat 0.8% oleamide, 1.2% lauric acid, 1% sodium nitrate, 65% water.
[0022] The preparation method of special grinding fluid, concrete steps are as follows:
[0023] ①Sodium petroleum sulfonate, sodium benzoate, monoethanolamine benzoate, polyether ester, molybdenum disulfide, dimethyl silicone oil, polyoxyethylene fatty acid ester, naphthenate, tricresyl phosphate, sulfurized fatty acid ester, oil Amide, triethanolamine, and lauric acid were added...
Embodiment 2
[0028] According to the following mass fractions: 2% engine oil, 1.5% soybean oil, 0.2% sodium petroleum sulfonate, 0.1% monoethanolamine benzoate, 0.1% sodium benzoate, 0.8% polyether ester, 1.5% simethicone , 2% molybdenum disulfide, 5% polyoxyethylene fatty acid ester, 0.2% chromium oleate, 0.2% triethanolamine, 0.5% benzisothiazolinone, 0.2% methyl benzotriazole, 2 % oxalic acid, 0.2% methyltrimethoxysilane, 0.2% sodium orthosilicate, 0.2% disodium hydrogen phosphate, 0.8% naphthenate, 4% tricresyl phosphate, 3% sulfurized fat It is prepared from 0.7% oleamide, 1% lauric acid, 0.8% sodium nitrate and 60% water.
[0029] The preparation method of special grinding fluid, concrete steps are as follows:
[0030] ①Sodium petroleum sulfonate, sodium benzoate, monoethanolamine benzoate, polyether ester, molybdenum disulfide, dimethyl silicone oil, polyoxyethylene fatty acid ester, naphthenate, tricresyl phosphate, sulfurized fatty acid ester, oil Amide, triethanolamine, and lau...
PUM
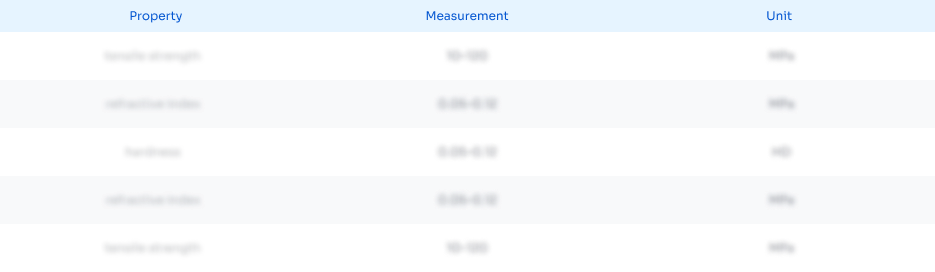
Abstract
Description
Claims
Application Information

- Generate Ideas
- Intellectual Property
- Life Sciences
- Materials
- Tech Scout
- Unparalleled Data Quality
- Higher Quality Content
- 60% Fewer Hallucinations
Browse by: Latest US Patents, China's latest patents, Technical Efficacy Thesaurus, Application Domain, Technology Topic, Popular Technical Reports.
© 2025 PatSnap. All rights reserved.Legal|Privacy policy|Modern Slavery Act Transparency Statement|Sitemap|About US| Contact US: help@patsnap.com