Combined leaching process of cobalt-sulfur concentrate and cobalt hydroxide ore
A technology of cobalt sulfur concentrate and cobalt hydroxide, applied in the direction of improving process efficiency, etc., can solve the problems of consuming liquid caustic soda, low liquid concentration, and large processing procedures
- Summary
- Abstract
- Description
- Claims
- Application Information
AI Technical Summary
Problems solved by technology
Method used
Image
Examples
Embodiment 1
[0061] This embodiment is a joint leaching process of cobalt sulfur concentrate and cobalt hydroxide ore, comprising the following steps:
[0062] S1. Raw material selection: see Table 4 for the chemical composition of the cobalt-sulfur concentrate in this example, and Table 5 for the chemical composition of the cobalt hydroxide ore.
[0063] Table 4 The present embodiment cobalt sulfur concentrate chemical composition (mass percentage (%))
[0064] element co Fe Ni Cu mn Zn SiO 2
S content / % 0.3 48.82 0.14 0.083 0.033 0.022 4.05 30.79
[0065] Table 5 present embodiment cobalt hydroxide ore chemical composition (mass percentage (%))
[0066] element co Fe Ni Cu mn Zn content / % 39.94 0.56 0.075 0.76 2.44 0.15
[0067] S2. Raw material pulping:
[0068] Cobalt sulfur concentrate, cobalt hydroxide ore and water are added to the pulping tank according to the mass ratio of 1:1:5, and after stirri...
Embodiment 2
[0081] This embodiment is a joint leaching process of cobalt sulfur concentrate and cobalt hydroxide ore, comprising the following steps:
[0082] S1. Raw material selection: See Table 7 for the chemical composition of the cobalt-sulfur concentrate in this example, and Table 8 for the chemical composition of the cobalt hydroxide ore.
[0083] Table 7 The present embodiment cobalt sulfur concentrate chemical composition (mass percentage (%))
[0084] element co Fe Ni Cu mn Zn SiO 2
S content / % 0.53 23.21 0.079 1.23 0.13 0.015 24.04 28.69
[0085] Table 8 present embodiment cobalt hydroxide ore chemical composition (mass percentage (%))
[0086] element co Fe Ni Cu mn Zn content / % 37.35 2.31 0.06 0.33 1.76 0.12
[0087] S2. Raw material pulping:
[0088] Cobalt sulfur concentrate, cobalt hydroxide ore and water are added to the pulping tank according to the mass ratio of 1:1:5, and after stirri...
PUM
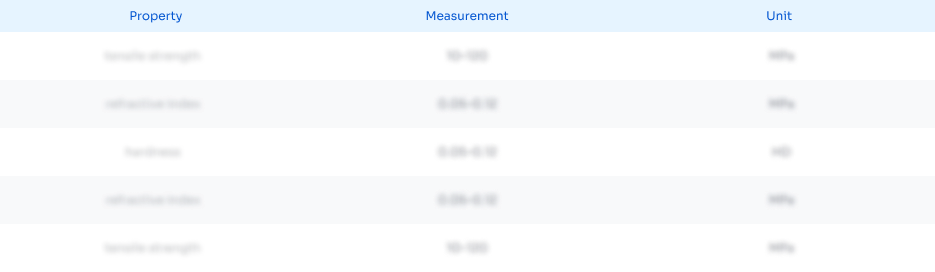
Abstract
Description
Claims
Application Information

- R&D Engineer
- R&D Manager
- IP Professional
- Industry Leading Data Capabilities
- Powerful AI technology
- Patent DNA Extraction
Browse by: Latest US Patents, China's latest patents, Technical Efficacy Thesaurus, Application Domain, Technology Topic, Popular Technical Reports.
© 2024 PatSnap. All rights reserved.Legal|Privacy policy|Modern Slavery Act Transparency Statement|Sitemap|About US| Contact US: help@patsnap.com