Production process for optimizing purity of corrosion-resistant alloy
A corrosion-resistant alloy and production process technology, which is applied in the field of corrosion-resistant alloy purity optimization production process, can solve the problems of poor stability of alloy performance level, low purity of corrosion-resistant alloy, etc., achieve fine-cast structure and improve seawater resistance Corrosion performance, effect of improving physical properties
- Summary
- Abstract
- Description
- Claims
- Application Information
AI Technical Summary
Problems solved by technology
Method used
Examples
Embodiment 1
[0024] The invention provides a technical solution: a process for optimizing the purity of corrosion-resistant alloys, comprising the following steps:
[0025] Step 1: In the annealing step of the raw material, the temperature of the first zone is 1050°C, the temperature range of the second zone is 1120°C, the temperature range of the third zone is 1120°C, the temperature range of the fourth zone is 1120°C, the temperature range of the fifth zone is 1120°C, and the temperature range of the sixth zone is The range is 1180°C;
[0026] Step 2: the pickling step of the raw material. The pickling step of the raw material is to pickle the slab after the annealing step of the raw material with a mixed acid, and the mixed acid is made of sulfuric acid, hydrochloric acid, nitric acid and water. And the mass fraction proportioning of sulfuric acid, hydrochloric acid, nitric acid is 2:3:1;
[0027] Step 3: the pre-press rolling step, the rolling pass of the pre-press rolling step is 18 ...
Embodiment 2
[0035] The invention provides a technical solution: a process for optimizing the purity of corrosion-resistant alloys, comprising the following steps:
[0036] Step 1: In the annealing step of the raw material, the temperature of the first zone is 1050°C, the temperature range of the second zone is 1120°C, the temperature range of the third zone is 1120°C, the temperature range of the fourth zone is 1120°C, the temperature range of the fifth zone is 1120°C, and the temperature range of the sixth zone is The range is 1180°C;
[0037] Step 2: the pickling step of the raw material. The pickling step of the raw material is to pickle the slab after the annealing step of the raw material with a mixed acid, and the mixed acid is made of sulfuric acid, hydrochloric acid, nitric acid and water. And the mass fraction proportioning of sulfuric acid, hydrochloric acid, nitric acid is 2:3:1;
[0038] Step 3: the pre-press rolling step, the rolling pass of the pre-press rolling step is 18 ...
Embodiment 3
[0046] The invention provides a technical solution: a process for optimizing the purity of corrosion-resistant alloys, comprising the following steps:
[0047] Step 1: In the annealing step of the raw material, the temperature of the first zone is 1050°C, the temperature range of the second zone is 1120°C, the temperature range of the third zone is 1120°C, the temperature range of the fourth zone is 1120°C, the temperature range of the fifth zone is 1120°C, and the temperature range of the sixth zone is The range is 1180°C;
[0048] Step 2: the pickling step of the raw material. The pickling step of the raw material is to pickle the slab after the annealing step of the raw material with a mixed acid, and the mixed acid is made of sulfuric acid, hydrochloric acid, nitric acid and water. And the mass fraction proportioning of sulfuric acid, hydrochloric acid, nitric acid is 2:3:1;
[0049] Step 3: the pre-press rolling step, the rolling pass of the pre-press rolling step is 18 ...
PUM
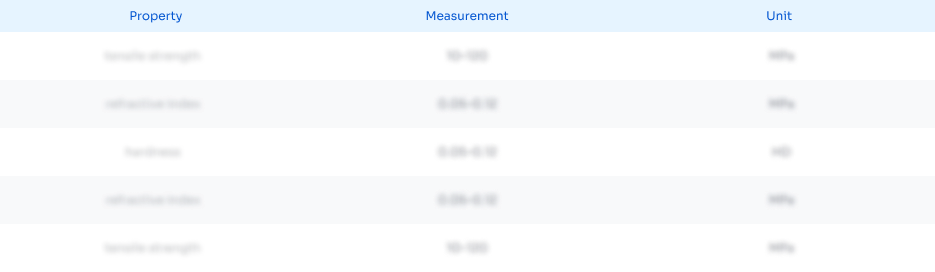
Abstract
Description
Claims
Application Information

- R&D Engineer
- R&D Manager
- IP Professional
- Industry Leading Data Capabilities
- Powerful AI technology
- Patent DNA Extraction
Browse by: Latest US Patents, China's latest patents, Technical Efficacy Thesaurus, Application Domain, Technology Topic, Popular Technical Reports.
© 2024 PatSnap. All rights reserved.Legal|Privacy policy|Modern Slavery Act Transparency Statement|Sitemap|About US| Contact US: help@patsnap.com