Slag-corrosion-resistant high-strength furnace-melting brick for gasification melting furnace and preparation method of furnace-melting brick
A gasification melting, high-strength technology, applied in the field of refractory materials, can solve the problems affecting the use effect and life, the performance of furnace melting bricks, etc., to improve the crystal stability and wear resistance, improve the resistance to slag corrosion The effect of promoting the uniformity of dispersion
- Summary
- Abstract
- Description
- Claims
- Application Information
AI Technical Summary
Problems solved by technology
Method used
Image
Examples
Embodiment 1
[0035] Example 1: A high-strength furnace fused brick for gasification and melting furnaces resistant to slag erosion. Its components include the following raw materials in parts by weight: 15 parts of skeleton, 30 parts of matrix, 1 part of external auxiliary agent and 6 parts of purified water;
[0036] The skeleton includes: 2 parts of coke gemstone, 3 parts of congealed stone, 2 parts of andalusite, 3 parts of magnesium-rich spinel, 3 parts of siliceous shale, and 2 parts of gibbsite;
[0037] The matrix includes: 15 parts of washed kaolin, α-Al 2 o3 2 parts of fine powder, 4 parts of zinc oxide, 4 parts of nano-carbon black, 3 parts of titanium dioxide, 2 parts of yttrium oxalate;
[0038] Added additives include: 0.2 parts of sintering aid, 0.2 parts of composite water reducer, and 0.6 parts of binder;
[0039] Among them: the sintering aid is CuMn30;
[0040] The composite water reducer is a mixture of polycarboxylic acid, sodium tripolyphosphate and sodium hexametaph...
Embodiment 2
[0052] Example 2: A high-strength furnace fused brick for a gasification melting furnace resistant to slag erosion, its composition includes the following raw materials in parts by weight: 30 parts of skeleton, 65 parts of matrix, 3 parts of external additives and 10 parts of purified water;
[0053] The skeleton includes: 4 parts of coke gemstone, 5 parts of congealed stone, 5 parts of andalusite, 5 parts of magnesium-rich spinel, 7 parts of siliceous shale, and 4 parts of gibbsite;
[0054] The matrix includes: 27 parts of washed kaolin, α-Al 2 o 3 4 parts of fine powder, 9 parts of zinc oxide, 7 parts of nano-carbon black, 11 parts of titanium dioxide, 7 parts of yttrium oxalate;
[0055] Added additives include: 0.8 parts of sintering aid, 0.7 parts of composite water reducer, and 1.5 parts of binder;
[0056] Among them: the sintering aid is CuMn30;
[0057] The composite water reducer is a mixture of polycarboxylic acid, sodium tripolyphosphate and sodium hexametaphos...
Embodiment 3
[0069] Example 3: A high-strength furnace fused brick for gasification and melting furnaces resistant to slag erosion, its composition includes the following raw materials in parts by weight: 23 parts of skeleton, 50 parts of matrix, 2 parts of external additives and 8 parts of purified water;
[0070] The skeleton includes: 3 parts of coke gemstone, 4 parts of congealed stone, 3 parts of andalusite, 4 parts of magnesium-rich spinel, 6 parts of siliceous shale, and 3 parts of gibbsite;
[0071] The matrix includes: 22 parts of washed kaolin, α-Al 2 o 3 3 parts of fine powder, 6 parts of zinc oxide, 6 parts of nano-carbon black, 7 parts of titanium dioxide, 6 parts of yttrium oxalate;
[0072] Added additives include: 0.5 part of sintering aid, 0.5 part of composite water reducer, 1.0 part of binder;
[0073] Among them: the sintering aid is CuMn30;
[0074] The composite water reducer is a mixture of polycarboxylic acid, sodium tripolyphosphate and sodium hexametaphosphate ...
PUM
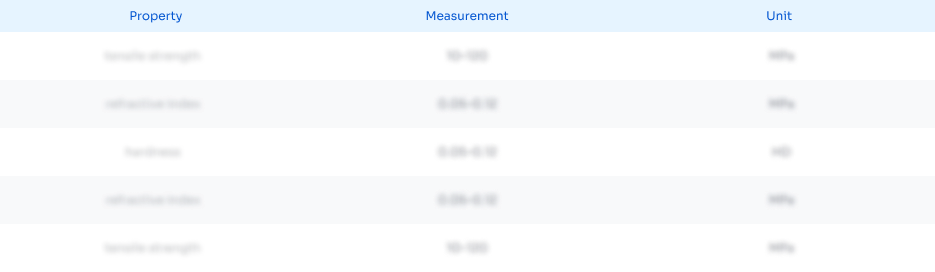
Abstract
Description
Claims
Application Information

- R&D
- Intellectual Property
- Life Sciences
- Materials
- Tech Scout
- Unparalleled Data Quality
- Higher Quality Content
- 60% Fewer Hallucinations
Browse by: Latest US Patents, China's latest patents, Technical Efficacy Thesaurus, Application Domain, Technology Topic, Popular Technical Reports.
© 2025 PatSnap. All rights reserved.Legal|Privacy policy|Modern Slavery Act Transparency Statement|Sitemap|About US| Contact US: help@patsnap.com