Ultra-pure tinplate and preparation method thereof
A tinplate, pure technology, applied in the field of iron and steel metallurgy, can solve the problems of improvement, inability to produce second phase, unfavorable mechanical properties of tinplate, etc.
- Summary
- Abstract
- Description
- Claims
- Application Information
AI Technical Summary
Problems solved by technology
Method used
Examples
preparation example Construction
[0031] In the preparation method of the ultra-pure tinplate of the present invention, the coarse deoxidation of the aluminum ingot is first carried out, and then the deep deoxidation of the aluminum after the titanium is carried out, specifically comprising the following steps:
[0032] (1) End point control of converter tapping
[0033] The tapping temperature of the converter is 1640-1660°C, P≤0.04%, and the amount of slag ≤4.2kg / t steel.
[0034] (2) Initial adjustment of molten steel composition
[0035] When the converter is tapped to 20% of the total volume of the ladle, add aluminum ingots for rough deoxidation, and at the same time add slag washing material for slag washing, and add it when the steel is tapped to 30% of the total volume of the ladle. When tapping reaches 50% of the total volume of the ladle, a binary alloy and a ternary alloy are added to the ladle for alloying. The binary alloy is a silicon-manganese alloy containing 20% to 25% by mass of silicon ...
Embodiment 1
[0042] The preparation method of the present embodiment ultra-pure tinplate comprises the following steps:
[0043] (1) End point control of converter tapping
[0044] The total mass of the converter is 100 tons, the tapping temperature is 1640-1660°C, the mass percentage of P is 0.04%, and the slag amount is 4.2kg / t steel.
[0045] (2) Initial adjustment of molten steel composition
[0046] When the converter is tapped to 20% of the total volume of the ladle, add aluminum ingots for rough deoxidation, and at the same time add slag washing material for slag washing, and add it when the steel is tapped to 30% of the total volume of the ladle. When the steel is tapped to 50% of the total volume of the ladle, silicon-manganese alloy and aluminum-manganese-ferroalloy are added to the steel ladle, wherein, in terms of mass percentages, the silicon-manganese alloy contains 25% by mass of silicon and 75% of manganese by mass; In the ferromanganese alloy, the mass content of aluminu...
Embodiment 2
[0056] The preparation method of the present embodiment ultra-pure tinplate comprises the following steps:
[0057] (1) End point control of converter tapping
[0058] The total mass of the converter is 120 tons, the tapping temperature is 1640-1660°C, the mass percentage of P is 0.03%, and the slag amount is 3.9kg / t steel.
[0059] (2) Initial adjustment of molten steel composition
[0060] When the converter is tapped to 20% of the total volume of the ladle, add aluminum ingots for rough deoxidation, and at the same time add slag washing material for slag washing, and add it when the steel is tapped to 30% of the total volume of the ladle. When the steel is tapped to 50% of the total volume of the ladle, silicon-manganese alloy and aluminum-manganese-ferroalloy are added to the steel ladle, wherein, in terms of mass percentages, the silicon-manganese alloy contains 22% by mass and 78% by mass of manganese; In the ferromanganese alloy, the mass content of aluminum, manganes...
PUM
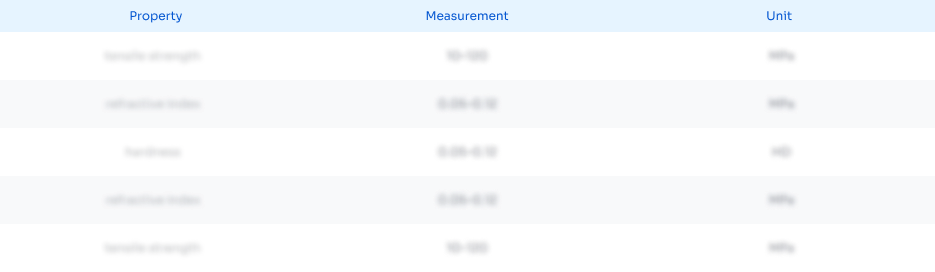
Abstract
Description
Claims
Application Information

- R&D Engineer
- R&D Manager
- IP Professional
- Industry Leading Data Capabilities
- Powerful AI technology
- Patent DNA Extraction
Browse by: Latest US Patents, China's latest patents, Technical Efficacy Thesaurus, Application Domain, Technology Topic, Popular Technical Reports.
© 2024 PatSnap. All rights reserved.Legal|Privacy policy|Modern Slavery Act Transparency Statement|Sitemap|About US| Contact US: help@patsnap.com