Glaze for ultrathin ceramic rock plate and preparation method and application of glaze
A technology for ceramics and rock slabs, which is applied in the field of glazes for ultra-thin ceramic rock slabs and its preparation, and can solve problems such as high prices, limited digital glaze covering power, and easy penetration of green bodies
- Summary
- Abstract
- Description
- Claims
- Application Information
AI Technical Summary
Problems solved by technology
Method used
Examples
Embodiment 1
[0072] A preparation method of a glaze for ultra-thin ceramic rock slabs of the present embodiment comprises the following steps:
[0073] Preparation of step S1 top glaze:
[0074] Step S11, add 13% ethylene glycol, 10% glycerin, 0.1% Surfynol 440, 0.1% Tego® Foamex 810, 0.3% BYK-410 and 3% self-made anhydrous polyacrylic acid dispersant into the vertical sand mill, Stir well to form a transparent solution 1.
[0075] Step S12, slowly add 20% albite, 9% dolomite, 5.5% bauxite, 5.5% zirconium silicate and 5% matte frit powder to transparent solution 1 (matte frit powder consists of 58% SiO 2 , 23% Al 2 o 3 , 5.6%K 2 O, 3.2% Na 2 O, 3% CaO, 5.2% MgO and 2% SrO), grind while stirring, the grinding medium is 1mm zirconia ball, grind to D 97 was 7.798 μm, and glaze suspension 1 was obtained.
[0076] Step S13, adding the remaining 18.5% ethylene glycol and 10% glycerin to the above glaze suspension 1 for performance adjustment, the adjusted glaze suspension 1 has a viscosi...
Embodiment 2
[0086] A preparation method of a glaze for ultra-thin ceramic rock slabs of the present embodiment comprises the following steps:
[0087] Preparation of step S1 top glaze:
[0088] Step S11, 9% ethylene glycol, 15% diethylene glycol, 0.15% Tego® Wet 505, 0.15% SN-Defoamer485, 0.5% Vok®-Keperrhevok-422 and 2.5% self-made anhydrous polyacrylic acid dispersant were added to In a vertical sand mill, stir evenly to form a transparent solution 1.
[0089] Step S12, slowly add 21% albite feldspar, 12% dolomite, 6% bauxite, 6% zirconium silicate and 3% matte frit powder to transparent solution 1 (matte frit powder consists of 63% SiO 2 , 20% Al 2 o 3 , 3%K 2 O, 4.2% Na 2 O, 4.2% CaO, 2% MgO and 3.6% SrO), grind while stirring, the grinding medium is 1mm zirconia ball, grind to D 97 was 9.237 μm, and glaze suspension 1 was obtained.
[0090] Step S13, adding the remaining 14.7% ethylene glycol and 10% diethylene glycol to the above glaze suspension 1 for performance adjustment...
Embodiment 3
[0100] A preparation method of a glaze for ultra-thin ceramic rock slabs of the present embodiment comprises the following steps:
[0101] Preparation of step S1 top glaze:
[0102] Step S11, mix 10% isopropanol, 14% glycerin, 5% diethylene glycol monobutyl ether, 0.15% Toynol® Superwet-300, 0.15% Tego® Foamex 810, 0.5% Vok®-Keperrhevok-422 and 3% Add the self-made anhydrous polyacrylic acid dispersant into a vertical sand mill, and stir evenly to form a transparent solution 1.
[0103] Step S12, slowly add 23% albite feldspar, 12% dolomite, 6% bauxite, 6% zirconium silicate and 5% matte frit powder to transparent solution 1 (matte frit powder consists of 62% SiO 2 , 21% Al 2 o 3 , 3%K 2 O, 3% Na 2 O, 4% CaO, 4% MgO and 3% SrO), grind while stirring, the grinding medium is 1mm zirconia ball, grind to D 97 was 7.337 μm, and glaze suspension 1 was obtained.
[0104] Step S13, adding the remaining 5.2% glycerin and 10% diethylene glycol monobutyl ether to the above-mentio...
PUM
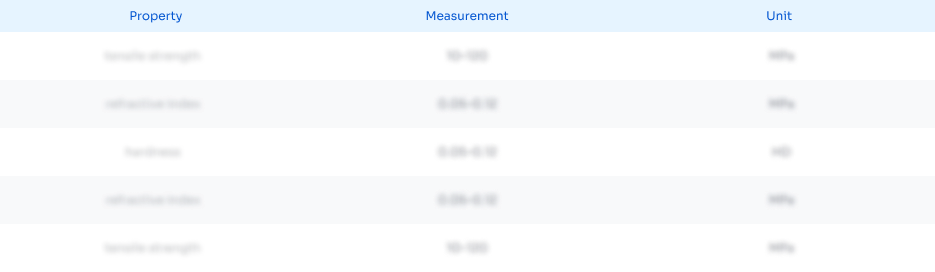
Abstract
Description
Claims
Application Information

- R&D Engineer
- R&D Manager
- IP Professional
- Industry Leading Data Capabilities
- Powerful AI technology
- Patent DNA Extraction
Browse by: Latest US Patents, China's latest patents, Technical Efficacy Thesaurus, Application Domain, Technology Topic, Popular Technical Reports.
© 2024 PatSnap. All rights reserved.Legal|Privacy policy|Modern Slavery Act Transparency Statement|Sitemap|About US| Contact US: help@patsnap.com