Atmosphere control powder metallurgy preparation method of graphene reinforced aluminum matrix composite
A technology for strengthening aluminum matrix and composite materials, applied in the field of metal matrix composite materials, can solve the problems of uncontrollable aluminum powder oxidation reaction, composite material failure, affecting the macroscopic plasticity of composite materials, etc., and achieve excellent mechanical and electrical properties and structural integrity. Good and beneficial to large-scale production
- Summary
- Abstract
- Description
- Claims
- Application Information
AI Technical Summary
Problems solved by technology
Method used
Image
Examples
Embodiment 1
[0062] This implementation provides a kind of graphene-enhanced aluminum matrix composite material (containing graphene 0.5wt.%) atmosphere control powder metallurgy preparation method, such as figure 1 As shown, the steps are as follows:
[0063] In a glove box with inert gas (argon) protection, take 99.5g, 10μm pure aluminum powder (spherical powder) and 0.5g graphene and place them in a planetary ball mill, add 1g stearic acid as a ball milling process control agent, and use stainless steel The ball is the ball milling medium, the ball-to-material ratio is 4:1, and the ball is milled at a speed of 500 rpm for 2 hours to obtain a graphene / aluminum composite powder, and the above composite powder is decomposed at 400°C under the same inert gas atmosphere. After gas treatment for 1 hour, hot press at 500°C and 600MPa for 1 hour to form a green body with a diameter of 40 mm (section as figure 2 shown in a). Take out the blank from the glove box, anneal at 300°C for 1 hour, a...
Embodiment 2
[0071] This implementation provides an atmosphere-controlled powder metallurgy preparation method of a graphene-enhanced aluminum matrix composite material (containing graphene 0.1wt.%), the steps are as follows:
[0072] In a glove box with inert gas (argon) protection, take 99.9g, 10μm pure aluminum powder (spherical powder) and 0.1g graphene and place them in a planetary ball mill, add 1g stearic acid as a ball milling process control agent, and use stainless steel The ball is the ball milling medium, the ball-to-material ratio is 4:1, and the ball is milled at a speed of 500 rpm for 2 hours to obtain a graphene / aluminum composite powder, and the above composite powder is decomposed at 400°C under the same inert gas atmosphere. After gas treatment for 1 hour, it was hot-pressed at 500°C and 600 MPa for 1 hour to form a green body with a diameter of 40 mm. Take out the blank from the glove box, anneal at 300°C for 1 hour in a muffle furnace, then hot-roll at 500°C to 1mm (70...
Embodiment 3
[0074] This implementation provides an atmosphere-controlled powder metallurgy preparation method of a graphene-enhanced aluminum-based composite material (graphene-containing 6wt.%), the steps are as follows:
[0075] Take 94g, 10μm pure aluminum powder (spherical powder) and 6g graphene in a glove box with inert gas protection (nitrogen) and place them in a planetary ball mill, add 1g stearic acid as a ball milling process control agent, and use stainless steel balls as ball milling Medium, the ball-to-material ratio is 4:1, and the graphene / aluminum composite powder is obtained by ball milling at a speed of 500 rpm for 2 hours. The above composite powder is degassed at 400°C for 1 hour under the same inert gas atmosphere. Afterwards, under the conditions of 500°C and 600MPa, it was hot-pressed for 1 hour to form a green body with a diameter of 40mm. The blank was taken out from the glove box, annealed at 300°C for 1 hour in a muffle furnace, then hot-rolled at 500°C to 1mm ...
PUM
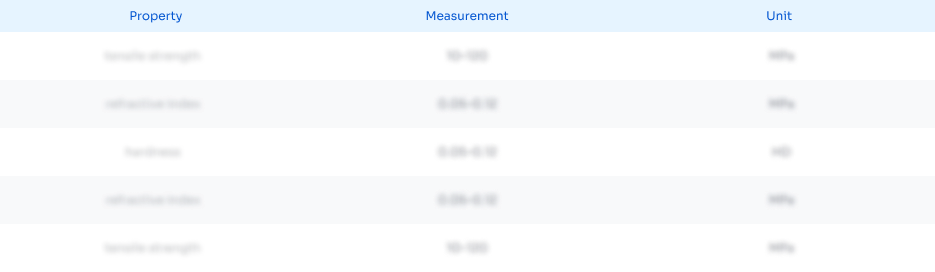
Abstract
Description
Claims
Application Information

- Generate Ideas
- Intellectual Property
- Life Sciences
- Materials
- Tech Scout
- Unparalleled Data Quality
- Higher Quality Content
- 60% Fewer Hallucinations
Browse by: Latest US Patents, China's latest patents, Technical Efficacy Thesaurus, Application Domain, Technology Topic, Popular Technical Reports.
© 2025 PatSnap. All rights reserved.Legal|Privacy policy|Modern Slavery Act Transparency Statement|Sitemap|About US| Contact US: help@patsnap.com