Quenching and tempering heat treatment process for improving flaw detection clutters of 2Cr13 rotor
A quenching and tempering heat treatment, 2cr13 technology, applied in heat treatment furnaces, heat treatment equipment, manufacturing tools, etc., can solve problems such as coarse rotor structure, difficult production operation control, and inability to effectively improve rotor flaw detection clutter problems, so as to avoid flaw detection Inconsistency, overall uniformity, and the effect of meeting market demand
- Summary
- Abstract
- Description
- Claims
- Application Information
AI Technical Summary
Problems solved by technology
Method used
Image
Examples
Embodiment 1
[0015] Example 1: A regulating heat treatment process for improving 2Cr13 rotor flawless waves: 2Cr13 chemical composition: C = 0.2%, Si = 0.3%, Mn = 0.59%, Cr = 12.55%, Ni = 0.29%, S = 0.003%, P = 0.014%, MO = 0.14%; Specifications: φ560mm step axis; flawless waves: 80% failed.
[0016] The heat treatment process step is specifically as follows:
[0017] Step 1), quenched: 12-meter deep well heating furnace production, the furnace temperature is controlled in ≤ 500 ° C, the temperature is warmed to 650 ± 20 ° C, and the temperature will be ≥100 ° C / h after heat temperature The temperature is warmed to 1000 ± 10 ° C for heat preservation, after the heat preservation is cooled, the air cooling time is 50s, the oil is 135min, the oil temperature is controlled in ≤50 ° C;
[0018] Step 2), high temperature tempering: When the step 1) is performed, the rotor is loaded into a 12-meter deep well heating furnace for high temperature tempering, the furnace temperature is controlled at ≤...
Embodiment 2
[0025] Example 2: An Improved Temperature Treatment Process, Steel Treatment: 2Cr13; Chemical Components: C = 0.22%, Si = 0.32%, Mn = 0.51%, Cr = 12.62%, Ni = 0.09% , S = 0.003%, P = 0.013%, MO = 0.04%; specifications: φ630mm step axis; flawless waves: 80% failed.
[0026] The tuning process is as follows:
[0027] Step 1), once quenched: 12-meter deep well heating furnace production, the furnace temperature is controlled in ≤ 500 ° C, the temperature is raised to 680 ± 20 ° C, and the temperature will be ≥100 ° C / h after heating speed after heat The temperature is warmed to 1000 ± 10 ° C for insulation, and after the insulation is 13h, the cooling time is released, and the air cooling time is 60 m, and then the oil temperature is 160 min, and the oil temperature is controlled in ≤50 ° C;
[0028] Step 2), high temperature tempering: When the step 1) is performed, load the rotor into 12 meters deep well heating furnace production, perform high temperature tempering, the furnace ...
PUM
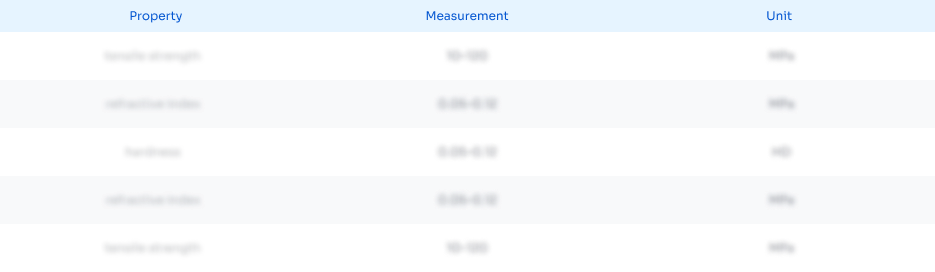
Abstract
Description
Claims
Application Information

- R&D Engineer
- R&D Manager
- IP Professional
- Industry Leading Data Capabilities
- Powerful AI technology
- Patent DNA Extraction
Browse by: Latest US Patents, China's latest patents, Technical Efficacy Thesaurus, Application Domain, Technology Topic, Popular Technical Reports.
© 2024 PatSnap. All rights reserved.Legal|Privacy policy|Modern Slavery Act Transparency Statement|Sitemap|About US| Contact US: help@patsnap.com