Remaining slag single-slag smelting operation method in converter low-iron-consumption mode
An operation method and converter technology, applied in the field of secondary copper production process equipment, can solve the problems of high consumption of iron and steel materials, insufficient phosphorus hit rate at the end of blowing, and achieve the effects of improving yield, stabilizing smelting cycle and improving hit rate.
- Summary
- Abstract
- Description
- Claims
- Application Information
AI Technical Summary
Problems solved by technology
Method used
Examples
Embodiment 1
[0033] Example 1 (steel type: rebar)
[0034] This embodiment provides a converter low iron consumption mode leaving slag single slag operation method, using a 130t converter (150t tapping capacity) blowing, the specific steps include:
[0035] S1. The weight percentage of raw material composition is: molten iron 80% (the main components in molten iron except iron are C: 4.79wt%, Si: 0.18wt%, P: 0.152wt%, molten iron temperature: 1350°C), scrap steel 12 %, pig iron 8%, the total amount of raw materials is 160.6t.
[0036] S2. After the slag splashing treatment, all the slag from the previous furnace is left in the converter, and the amount of slag remaining is 5t, and then the above-mentioned raw materials are added into the furnace to prepare for smelting.
[0037] S3. During smelting, during the blowing stage, lower the position of the oxygen lance to 1550-1650mm, adjust the flow rate of the oxygen lance to 38000m3 / h, lower the oxygen lance to 1300mm after igniting and blowin...
Embodiment 2
[0041] Example 2 (steel type: common low-quality)
[0042] S1. The weight percentage of raw material composition is: molten iron 75% (the main components in molten iron except iron are C: 4.51wt%, Si: 0.49wt%, P: 0.135wt%, molten iron temperature: 1280°C), scrap steel 16 %, pig iron 9%, the total amount of raw materials is 162t.
[0043] S2. After the slag splashing treatment, all the slag from the previous furnace is left in the converter, and the amount of slag remaining is 4.3t. Then the above raw materials are added into the furnace to prepare for smelting.
[0044] S3. During smelting, during the blowing stage, lower the position of the oxygen lance to 1550-1650mm, adjust the flow rate of the oxygen lance to 35000m3 / h, ignite the fire and start blowing for 150s, then move the oxygen lance down to 1300mm, and start adding 2000kg of lime , magnesium ball 850kg;
[0045] S4. When the blowing is about 5 minutes, the slag is active. Adjust the flow rate of the oxygen lance t...
Embodiment 3
[0048] Example 3 (steel type: low-carbon and low-phosphorus steel)
[0049] S1. The weight percentage of raw material composition is: molten iron 70% (main components in molten iron except iron are C: 4.63wt%, Si: 0.36wt%, P: 0.130wt%, molten iron temperature: 1349°C), scrap steel 21%, pig iron 9%, the total amount of raw materials is 166.4t.
[0050] S2. The slag from the previous furnace is left in the converter after half slag pouring and slag splashing treatment, the amount of slag remaining is 5.3t, and then the above raw materials are added into the furnace to prepare for smelting.
[0051] S3. During smelting, during the blowing stage, lower the position of the oxygen lance to 1550-1650mm, adjust the flow rate of the oxygen lance to 36000m3 / h, ignite the fire and start blowing for 150s, then move the oxygen lance down to 1300mm, and start adding lime 2400kg , magnesium ball 1500kg;
[0052] S4. When the blowing is about 5 minutes, the slag is active. Adjust the flow r...
PUM
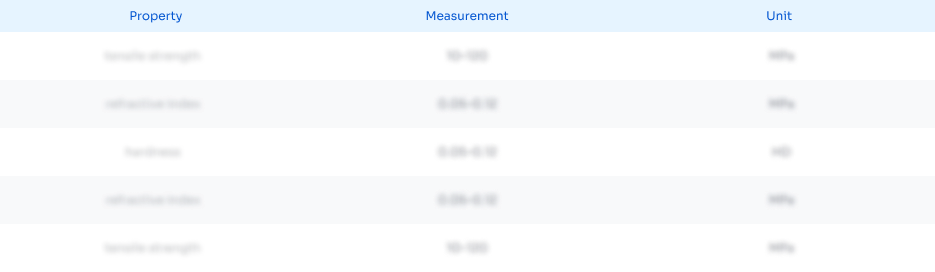
Abstract
Description
Claims
Application Information

- R&D Engineer
- R&D Manager
- IP Professional
- Industry Leading Data Capabilities
- Powerful AI technology
- Patent DNA Extraction
Browse by: Latest US Patents, China's latest patents, Technical Efficacy Thesaurus, Application Domain, Technology Topic, Popular Technical Reports.
© 2024 PatSnap. All rights reserved.Legal|Privacy policy|Modern Slavery Act Transparency Statement|Sitemap|About US| Contact US: help@patsnap.com