Production method for polycarbonate
A polycarbonate and halogenated hydrocarbon technology, applied in the field of polycarbonate preparation, can solve the problems of expensive, unsuitable for mass production, etc.
- Summary
- Abstract
- Description
- Claims
- Application Information
AI Technical Summary
Problems solved by technology
Method used
Image
Examples
preparation example Construction
[0069] In the preparation method of polycarbonate of the present invention, in the presence of oxygen to contain C 1-4 A composition of a halogenated hydrocarbon, a diol compound, and a specific base is irradiated with light.
[0070] 1.C 1-4 Halogenated hydrocarbon
[0071] In the reaction of the present invention, it is considered that C 1-4 Halogenated hydrocarbons may be decomposed by irradiation of light and oxygen, converted into carbonyl halides or compounds similar to carbonyl halides, and react with diol compounds to form polycarbonates. Even if harmful carbonyl halides are generated, the carbonyl halides immediately react with the diol compound due to their extremely high reactivity, and do not leak out of the reaction solution, or even if they leak, the amount of leakage is small. For example, phosgene as a carbonyl halide has very high toxicity and imposes severe restrictions on its transport, etc., but C 1-4 Halogenated hydrocarbons are certainly not terribly ...
Embodiment 1
[0198] Embodiment 1: the synthesis of BisP-CDE polycarbonate
[0199] [chemical formula 16]
[0200]
[0201] A quartz glass sleeve with a diameter of 30 mm is placed in a cylindrical reaction vessel with a diameter of 42 mm and a capacity of 100 mL, and then a low-pressure mercury lamp (“UVL20PH-6” produced by SEN Light Company, 20 W, ), build a reaction system. figure 1 A schematic diagram of the reaction system is shown. In addition, the irradiation light from this low-pressure mercury lamp contains UV-C with a wavelength of 254 nm, and the illuminance of the light with a wavelength of 254 nm at a position 5 mm from the tube wall is 6.23 to 9.07 mW / cm 2 . Refined chloroform (20mL), 4,4'-cyclododecylphenylene bisphenol (BisP-CDE, produced by Honshu Chemical Industry Co., Ltd.) (3.52g, 10mmol), 5 times the molar ratio of BisP-CDE Pyridine (4.04 mL) was added to the reaction vessel and stirred to mix. While stirring the reaction solution, 1 L / min of oxygen gas was bub...
Embodiment 2
[0212] Embodiment 2: the synthesis of BisP-CDE polycarbonate
[0213] In the reaction vessel of the reaction system used in Example 1, purified chloroform (20 mL), BisP-CDE (3.52 g, 10 mmol) and aqueous sodium hydroxide solution (NaOH: 8 g, 50 mL, 200 mmol) were added, and stirred and mixed. While stirring the reaction liquid, 1 L / min of oxygen gas was bubbled in at 20° C., and the above-mentioned low-pressure mercury lamp was irradiated for 1 hour.
[0214] Dichloromethane was added to the reaction solution for liquid separation, and the organic phase was dehydrated with anhydrous sodium sulfate, followed by concentration to obtain a brown oil (amount: 5.87 g, yield: >100%). As a result of analyzing the obtained solid by 1H NMR, it was confirmed that the target compound was produced although dichloromethane was mixed. In addition, the yield exceeding 100% was due to the residue of the solvent.
[0215] The molecular weight of the obtained BisP-CDE polycarbonate was determin...
PUM
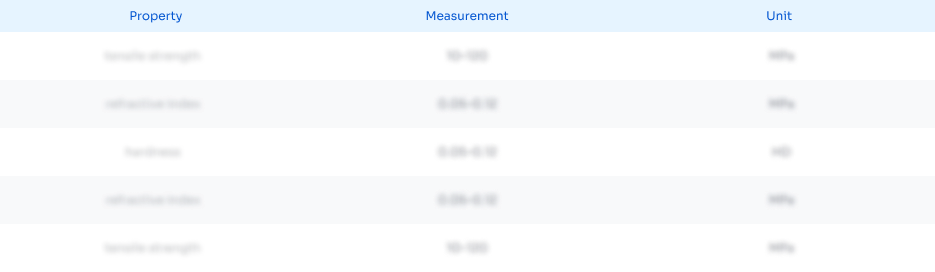
Abstract
Description
Claims
Application Information

- R&D Engineer
- R&D Manager
- IP Professional
- Industry Leading Data Capabilities
- Powerful AI technology
- Patent DNA Extraction
Browse by: Latest US Patents, China's latest patents, Technical Efficacy Thesaurus, Application Domain, Technology Topic, Popular Technical Reports.
© 2024 PatSnap. All rights reserved.Legal|Privacy policy|Modern Slavery Act Transparency Statement|Sitemap|About US| Contact US: help@patsnap.com