Method for improving compressive strength of alkaline pellets prepared from limestone
A technology of alkaline pellets and compressive strength, which is applied in the field of improving the compressive strength of alkaline pellets with limestone, and can solve problems such as affecting the compressive strength of pellets, increasing energy consumption, and excessive liquid
- Summary
- Abstract
- Description
- Claims
- Application Information
AI Technical Summary
Problems solved by technology
Method used
Examples
Embodiment 1
[0022] A method for improving the compressive strength of alkaline pellets with limestone, comprising the steps of:
[0023] In the first step, add 2.5 parts by weight of anhydrous magnesium sulfate and 17.12 parts by weight of urea into deionized water, stir evenly, add 0.2 parts by weight of sodium polyacrylate, stir magnetically for 1 hour, and prepare a mixed solution, and then transfer the mixed solution to the reaction kettle , stirred at a constant speed at 150°C and reacted for 6 hours, cooled to room temperature after the reaction, filtered, washed, and dried to obtain the precursor, then placed the precursor in a muffle furnace, roasted at 500°C for 5 hours, and cooled to obtain Treated magnesium oxide;
[0024] In the second step, 0.5 parts by weight of processed magnesium oxide, 2.3 parts by weight of calcium oxide and 55 parts by weight of fine iron ore are uniformly mixed, pulverized and ground until the particle size is 1mm, and mixed ore powder is obtained;
...
Embodiment 2
[0029] A method for improving the compressive strength of alkaline pellets with limestone, comprising the steps of:
[0030] In the first step, add 2.8 parts by weight of anhydrous magnesium sulfate and 17.35 parts by weight of urea into deionized water, stir evenly, add 0.4 parts by weight of sodium polyacrylate, stir magnetically for 1 hour, and prepare a mixed solution, and then transfer the mixed solution to the reaction kettle , stirred at a constant speed at 150°C and reacted for 6 hours, cooled to room temperature after the reaction, filtered, washed, and dried to obtain the precursor, then placed the precursor in a muffle furnace, roasted at 500°C for 5 hours, and cooled to obtain Treated magnesium oxide;
[0031] In the second step, 1.0 parts by weight of processed magnesium oxide, 3.0 parts by weight of calcium oxide and 60 parts by weight of fine iron ore are uniformly mixed, pulverized and ground until the particle size is 3mm, and mixed ore powder is obtained;
...
Embodiment 3
[0036]A method for improving the compressive strength of alkaline pellets with limestone, comprising the steps of:
[0037] In the first step, add 3.0 parts by weight of anhydrous magnesium sulfate and 17.56 parts by weight of urea into deionized water, stir evenly, add 0.5 parts by weight of sodium polyacrylate, stir magnetically for 1 hour, and prepare a mixed solution, and then transfer the mixed solution to the reaction kettle , stirred at a constant speed at 180°C and reacted for 6 hours, cooled to room temperature after the reaction, filtered, washed, and dried to obtain a precursor, then placed the precursor in a muffle furnace, roasted at 550°C for 5 hours, and cooled to obtain Treated magnesium oxide;
[0038] In the second step, 2.0 parts by weight of processed magnesium oxide, 3.5 parts by weight of calcium oxide and 70 parts by weight of fine iron ore are uniformly mixed, pulverized and ground until the particle size is 5mm, and mixed mineral powder is obtained;
...
PUM
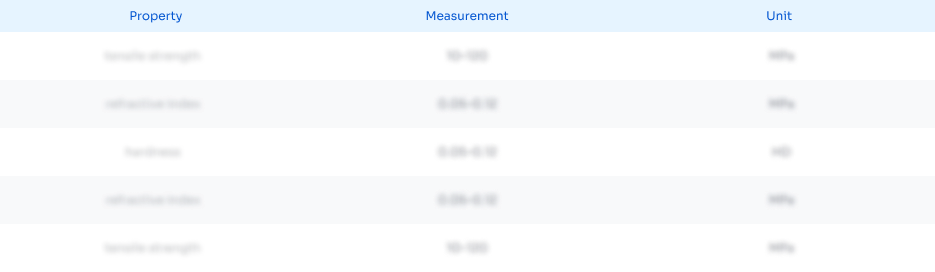
Abstract
Description
Claims
Application Information

- R&D Engineer
- R&D Manager
- IP Professional
- Industry Leading Data Capabilities
- Powerful AI technology
- Patent DNA Extraction
Browse by: Latest US Patents, China's latest patents, Technical Efficacy Thesaurus, Application Domain, Technology Topic, Popular Technical Reports.
© 2024 PatSnap. All rights reserved.Legal|Privacy policy|Modern Slavery Act Transparency Statement|Sitemap|About US| Contact US: help@patsnap.com