Hot galvanizing plastic dipping coating method
A hot-dip galvanizing and coating technology, applied in coating, metal material coating technology and other directions, can solve the problems of high environmental pressure, poor phosphating film polarity, insufficient polyethylene binding force, etc., to avoid structural defects, improve The effect of bonding
- Summary
- Abstract
- Description
- Claims
- Application Information
AI Technical Summary
Problems solved by technology
Method used
Image
Examples
Embodiment 1
[0047](1) Silane treatment: a silane coupling agent (vinyl trimethoxysilane): deionized water: methanol = 1: 10: 2 is good, add methanol in deionized water, placed in a magnetic stirrer The stirring is mixed, the silane coupling agent is slowly added, and the pH is added dropwise to 4.5 to 4.5, and the solution is continued to be transparent and uniform, and the solution is allowed to obtain a silane coupling agent; The silane coupling agent hydrolyzed solution is sprayed onto a hot galvanized wire, and the spray amount is 22L / m. 2 The silane coupling agent hydrolyzed solution is currently available;
[0048] (2) Drying Preheating: The hot-dip galvanized wire net sprayed silane coupling agent hydrolyzed solution is 15 min at 240 ° C to form a silane film to obtain a drying prevention.
[0049] (3) Immersion: impregnate the drying precipitation of polyethylene powder, the vibration is removed, and the immersion is obtained;
[0050] (4) Curing: Put the dip plastic into the curing...
Embodiment 2
[0053] According to the process step of Example 1, the drying precipitation temperature was changed to 220 ° C, and the drying time was 20 min; the cure temperature was 160 ° C, time 20 min. After the hot-dip galvanized wire is immersed, the polyethylene coating adhesion reaches 1 (GB / T9286-88).
Embodiment 3
[0055] According to the flow step of Example 1, the drying precipitation temperature was changed to 200 ° C, and the drying time was changed to 30 min; the curing temperature was 180 ° C, and time 20 min. After the hot-dip galvanized wire mesh is plasticized, the polyethylene coating adhesion can reach level 1 (GB / T9286-88).
PUM
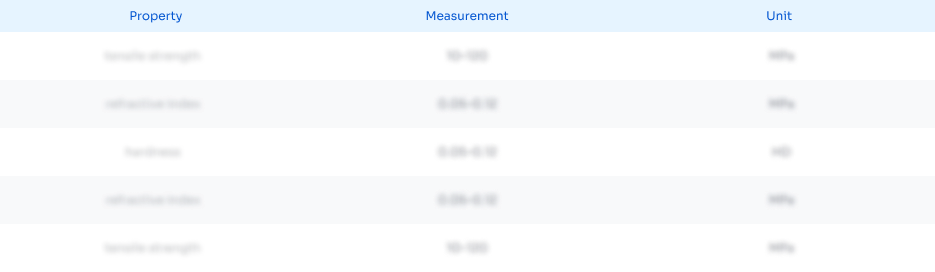
Abstract
Description
Claims
Application Information

- R&D
- Intellectual Property
- Life Sciences
- Materials
- Tech Scout
- Unparalleled Data Quality
- Higher Quality Content
- 60% Fewer Hallucinations
Browse by: Latest US Patents, China's latest patents, Technical Efficacy Thesaurus, Application Domain, Technology Topic, Popular Technical Reports.
© 2025 PatSnap. All rights reserved.Legal|Privacy policy|Modern Slavery Act Transparency Statement|Sitemap|About US| Contact US: help@patsnap.com