Method for preparing carbon monoxide low-shift catalyst by far infrared roasting
A far-infrared and carbon monoxide technology is applied in the field of preparation of carbon monoxide low-change catalysts, which can solve the problems of catalyst sintering, insufficient material decomposition, large temperature fluctuations, etc., and achieve the effects of stable catalyst performance, ideal pore structure, and uniform loss on ignition.
- Summary
- Abstract
- Description
- Claims
- Application Information
AI Technical Summary
Problems solved by technology
Method used
Image
Examples
Embodiment 1
[0036] The copper-zinc-aluminum ternary material is obtained by a precipitation method, and a wet filter cake is obtained after washing and filtering. The wet filter cake is processed, dried and rolled. Weigh 400 kg of dry material (the basic parameters of the material are guaranteed to be consistent), put it into the far-infrared storage tank, adjust and set the temperature of each temperature control zone to 330°C, set the control speed to 550r / min, and adjust the feeding amount to 100Kg / h. Adjust the scraper of the feeding trough, and discharge the material at a constant speed, so that the average thickness of the material on the chain plate belt is 20mm±2㎜, run for 2 hours, and take samples for analysis.
Embodiment 2
[0038] The copper-zinc-aluminum ternary material is obtained by a precipitation method, and a wet filter cake is obtained after washing and filtering. The wet filter cake is processed, dried and rolled. Weigh 400 kg of dry material (the basic parameters of the material are guaranteed to be consistent), put it into the far-infrared storage tank, adjust and set the temperature of each temperature control zone to 350°C, set the control speed to 550r / min, and adjust the feeding amount to 100Kg / h. Adjust the scraper of the feeding trough, and discharge the material at a constant speed, so that the average thickness of the material on the chain plate belt is 20mm±2㎜, run for 2 hours, and take samples for analysis.
Embodiment 3
[0040] The copper-zinc-aluminum ternary material is obtained by a precipitation method, and a wet filter cake is obtained after washing and filtering. The wet filter cake is processed, dried and rolled. Weigh 400 kg of dry material (the basic parameters of the material are guaranteed to be consistent), put it into the far-infrared material storage tank, adjust and set the temperature of each temperature control zone to 320°C, set the control speed to 600r / min, and adjust the feeding amount to 100Kg / h. Adjust the scraper of the feeding trough, and discharge the material at a constant speed, so that the average thickness of the material on the chain plate belt is 20mm±2㎜, run for 2 hours, and take samples for analysis.
PUM
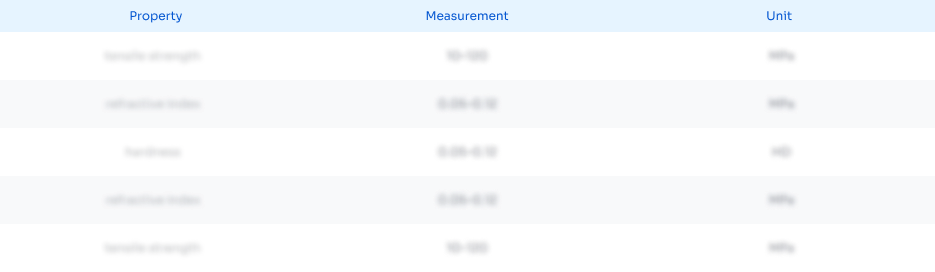
Abstract
Description
Claims
Application Information

- Generate Ideas
- Intellectual Property
- Life Sciences
- Materials
- Tech Scout
- Unparalleled Data Quality
- Higher Quality Content
- 60% Fewer Hallucinations
Browse by: Latest US Patents, China's latest patents, Technical Efficacy Thesaurus, Application Domain, Technology Topic, Popular Technical Reports.
© 2025 PatSnap. All rights reserved.Legal|Privacy policy|Modern Slavery Act Transparency Statement|Sitemap|About US| Contact US: help@patsnap.com